骨料的筛分、聚氨酯筛板
مزاياألواحشاشة البولي يوريثينفي غربلةالركام
يلعبفحصالركامدورًا محوريًافيالعمليات الصناعيةالمختلفة، حيث يتم فصل المواد على أساسالحجموالشكل لتلبيةمتطلباتمحددة。 تعتبرهذهالعملية أساسيةفيقطاعاتمثل التعدينوالبناء وإعادةالتدوير،حيث تكونجودةالمواد واتساقهاأمرًابالغ الأهمية。 منبينالموادالمختلفة المستخدمةفيألواح الغربلة، برزالبولي يوريثينكخيارمتميز، حيث يوفر عددًا كبيرًا منالمزايامقارنة بالمواد التقليديةمثل الفولاذأوالمطاط。 تتعمقهذهالمقالةفي فوائد ألواح شاشات البولي يوريثينفي الفحصالكلي،وتسلط الضوءعلىسببتزايد شعبيتهافيالسنوات الأخيرة。
تشتهرلوحات شاشات البولي يوريثين بمتانتهاالاستثنائية ومقاومتهاللتآكل。 علىعكسالشاشات المعدنيةالتييمكنأن تتآكلأوالشاشات المطاطيةالتيقدتتحلل بمرورالوقت،يتحمل البولي يوريثينالظروف القاسية،بمافيذلك التعرضللزيوتوالماء والأشعةفوقالبنفسجية。 وتترجمهذهالمرونةإلى عمرأطول،ممايقلل الحاجةإلىعمليات استبدالمتكررة، وبالتاليخفضتكاليف التشغيل。 علاوةعلىذلك،تضمن متانة مادة البولي يوريثينأداءًمتسقًا في عمليات الفحص، والحفاظعلىالكفاءة والإنتاجيةبمرور الوقت。
ميزةأخرىمهمة لألواح شاشة البولي يوريثينهيمقاومتها الفائقةللتآكل。 فيالبيئةالكاشطة لغربلة الركام، حيث تحتكالموادباستمرار بالشاشة، تظهر ألواح البولي يوريثينقدرة تحململحوظة。 لاتعملهذهالمقاومة للتآكلعلىإطالةعمر الشاشةفحسب،بلتحافظ أيضًاعلىسلامةسطح الغربلة،ممايضمن تحديد الحجم الدقيق للموادوفصلها。 ويعني انخفاضالتآكل أيضًاأنشاشاتالبولي يوريثينأقلعرضة لتكوينثقوبأوتمزقات، مما قد يؤدي إلى تلوث المواد التي يتم فحصها أوتتطلبوقتًامكلفًا للتوقفعنالعمل للإصلاحات。
توفرلوحات شاشات البولي يوريثين أيضًامرونةمعززة مقارنةبنظيراتها الصلبة。 تسمح هذهالمرونة للألواح بامتصاص الصدمات بشكل أفضل، مما يقللمناحتماليةالكسر عند التعامل مع المواد الكبيرةأوالحادة。 علاوةعلىذلك،فإن الطبيعةالمرنةللبولي يوريثينتسهلآلية التنظيفالذاتي،حيث تنثني الشاشةلطرد الجزيئات العالقة، وبالتاليتقليل الانسدادوالحفاظعلى كفاءةالفحصالمثلى。 تعدخاصيةالتنظيف الذاتي هذه مفيدةبشكل خاصفيالتطبيقاتالتي تتعاملمعالمواد الرطبةأواللزجة،حيث يمكنأنيؤديالانسداد إلىإعاقةالأداءبشكل كبير。
بالإضافةإلىفوائدها الوظيفية، تساهملوحات الشاشةالمصنوعةمن البولي يوريثينفي تقليلالضوضاءأثناء عملياتالفحص。 تساعدخصائصتخفيف الصوت المتأصلةفي المادةعلىامتصاص الصوت وتبديده، مما يؤدي إلى بيئة عمل أكثر هدوءًا。 لايؤديهذاالانخفاضفي التلوث الضوضائي إلى تعزيزراحةالعمال وسلامتهمفحسب،بل يتوافقأيضًامع اللوائح الصارمةبشكل متزايد بشأن مستويات الضوضاءفيمكان العمل。
أخيرًا،توفر لوحات شاشات البولي يوريثينتنوعًافي التصميموالتخصيص。 يمكنللمصنعينإنتاج الألواح بمجموعةواسعة منالأحجاموالأشكال والتكويناتلتناسب معدات وتطبيقات الفحص المختلفة。 تضمنهذهالقدرةعلى التكيفأنيتمكن المشغلونمنتحسين عمليات الفحصالخاصة بهم، وتحقيق كفاءة أعلى وفصلأفضلللمواد。 وتسمحالقدرةعلىتخصيص حجم ونمط الفتحة أيضًا بالتحكمالدقيقفي نتائج الفحص، بما يلبي خصائصومتطلباتالمواد المحددة.
مقارنةكفاءة الغربلة:ألواحالبولي يوريثينمقابلوسائط الغربلةالتقليدية
ميزةأخرىمهمةلألواح البولي يوريثينهي قدرتهاعلىتقليل الضوضاء。 يمكنأنتكونعملية الفحصعاليةبشكل استثنائي،خاصةمع الشاشات المعدنية، مما قد يخلق بيئة عمل مليئة بالتحديات وقد يتطلب استثمارًاإضافيًافي تدابيرالتحكمفي الضوضاء。 تساهمخصائصالبولي يوريثينالمتأصلةفي تخفيفالصوتفيتشغيل أكثرهدوءًا،وتعزيز بيئةالعملوربماتقليل الحاجة إلى حلول مكلفة لتقليلالضوضاء。
ومع ذلك، من المهم الاعتراف بأنألواحالبولي يوريثين،علىالرغممن كونهامفيدةفيكثيرمن النواحي، قد تأتي تكلفة أوليةأعلىمقارنةببعض الوسائطالتقليدية。 يمكنأنيكونهذا الاستثمارالأولي رادعًالبعضالعمليات، خاصةتلكالتيتخضع لقيودصارمةفي الميزانية。 ومع ذلك، فإن وفورات التكلفةعلىالمدى الطويلبسببانخفاض الصيانة،وتكرار الاستبدال،ووقت التوقفعنالعملغالبًا ماتبررالنفقات الأوليةللعديدمن المستخدمين。
في المقابل، قد توفر وسائط الفحصالتقليدية،مثل الشبكات السلكية، تكلفةأوليةأقلولكنها قدتتكبدارتفاع النفقات بمرورالوقت بسببالتآكل والاستبدالالمتكرر وخسائرالإنتاج المحتملةبسببالفحص غيرالمتسق。 بالإضافةإلىذلك،يمكن أنتكونالشاشات المعدنيةعرضةللتآكل، ممايقللمنعمرها الافتراضي وفعاليتها في بيئات معينة。
تتأثركفاءةوسائط الفحصأيضًابعواملمثل سعةالحمولةوتدفق المواد。 تسمح مرونة مادة البولي يوريثينبامتصاص الطاقةوتقليلالتأثير على سطح الشاشة، مما يمكنأنيعززسعة التحميلويحسنتدفق الموادعبرالشاشة。 يمكن أن يؤدي هذا إلى فحص أكثركفاءةمعتقليل ترحيلالموادوالتلوث。
إنمتانتهوخيارات التخصيصوتقليل الضوضاءوفعالية التكلفةالإجمالية تجعلهخيارًامقنعًا للعمليات التي تسعىإلى تحسينعملياتالفحص الخاصةبها。 فيحينأنالتكلفة الأوليةقدتكونأعلى، فإنالفوائدطويلة المدىوالتحسينات التشغيليةالتيتوفرها ألواح البولي يوريثين غالبًاماتؤديإلىعائد مناسبعلىالاستثمار، ممايجعلهاخيارًا قابلاً للتطبيقوذو شعبيةمتزايدةفيصناعة الغربلةالإجمالية。
标题:比较筛选效率:聚氨酯板与传统筛选介质
在材料分离和尺寸分类领域,筛选效率至关重要。筛分介质的选择显着影响最终产品的质量、筛分设备的使用寿命以及总体运营成本。在各种可用的选择中,聚氨酯筛板已成为传统筛网(例如金属丝网、钢板和橡胶筛网)的值得注意的替代品。这种比较旨在阐明聚氨酯面板与传统同类产品之间的区别,突出各自固有的优势和潜在局限性。
聚氨酯筛板以其耐用性和高耐磨性而闻名,这是筛分应用中的关键因素,涉及恶劣的材料。与会很快磨损或堵塞的传统金属丝网不同,聚氨酯的弹性使其能够抵抗冲击并避免颗粒堵塞筛分表面的堵塞。这种弹性不仅可以延长筛网的使用寿命,还可以保持稳定的吞吐量,这对于高效操作至关重要。
此外,聚氨酯面板设计有多种孔径形状和尺寸,可以根据特定的材料特性和筛分要求进行定制。这种定制有助于改善材料分层和分离,从而提高产品质量。相比之下,传统培养基的灵活性可能较低,需要做出妥协,这可能会导致筛选性能不佳。
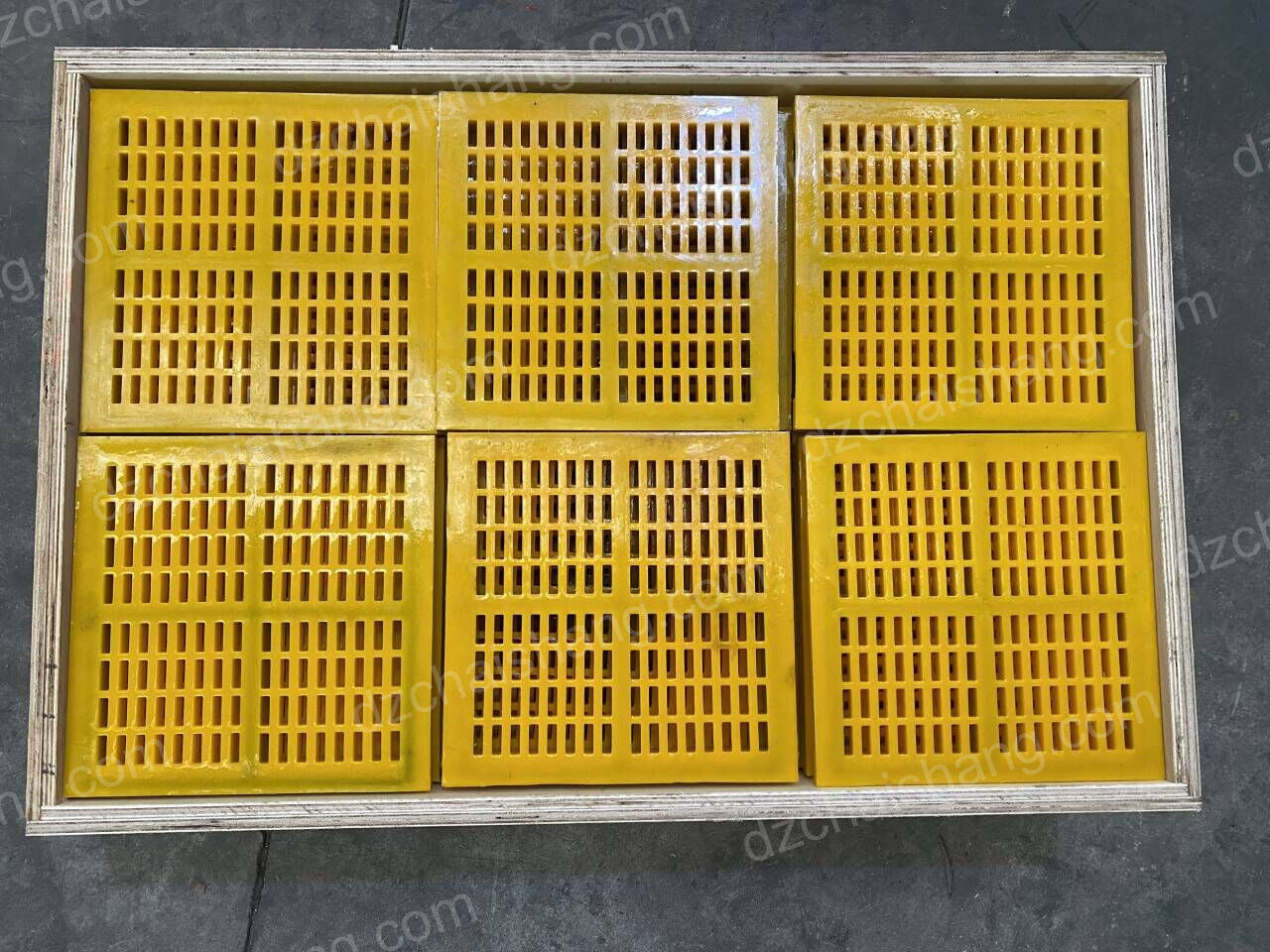
聚氨酯板的另一个显着优势是其降噪能力。筛选过程可能会非常吵闹,尤其是金属筛选,这可能会造成一个具有挑战性的工作环境,并且可能需要在噪音控制措施方面进行额外投资。聚氨酯固有的隔音特性有助于实现更安静的操作,改善工作环境,并有可能减少对昂贵的降噪解决方案的需求。
然而,重要的是要认识到,聚氨酯面板虽然在许多方面都有优势,但可能会带来一些问题。与某些传统媒体相比,初始成本更高。这种前期投资可能会阻碍某些业务,特别是那些预算紧张的业务。然而,由于减少维护、更换频率和停机时间而节省的长期成本通常证明许多用户的初始支出是合理的。
相比之下,传统的筛分介质(如金属丝网)可能提供较低的初始成本,但可能会产生额外的费用。随着时间的推移,由于磨损、频繁更换以及筛选不一致造成的潜在生产损失,费用会增加。此外,金属筛网容易腐蚀,从而进一步缩短其在某些环境下的使用寿命和有效性。
筛分介质的效率还受到负载能力和物料流等因素的影响。聚氨酯的柔韧性使其能够吸收能量并减少对筛板的冲击,从而可以增强负载能力并改善穿过筛板的物料流动。这可以实现更高效的筛分,同时减少材料残留和污染。
总之,当将聚氨酯筛板与传统筛分介质进行比较时,很明显,聚氨酯具有多种优势,可以提高筛分效率。其耐用性、定制选项、降噪和整体成本效益使其成为寻求优化筛选流程的运营商的绝佳选择。虽然初始成本可能较高,但聚氨酯板提供的长期效益和操作改进通常会带来良好的投资回报,使其成为骨料筛分行业中可行且越来越受欢迎的选择。