振动聚氨酯直线振动筛骨料、橡胶张力甲板OEM
مزاياشاشات الاهتااا الخطيةمنمادةالبdووو يوريثينفيالمعالجج الإجمالية
الابتكارات في أسطح التوترالمطاطية لتطبيقات الشاشات الاهتزازيةلتصنيع المعدات الأصلية
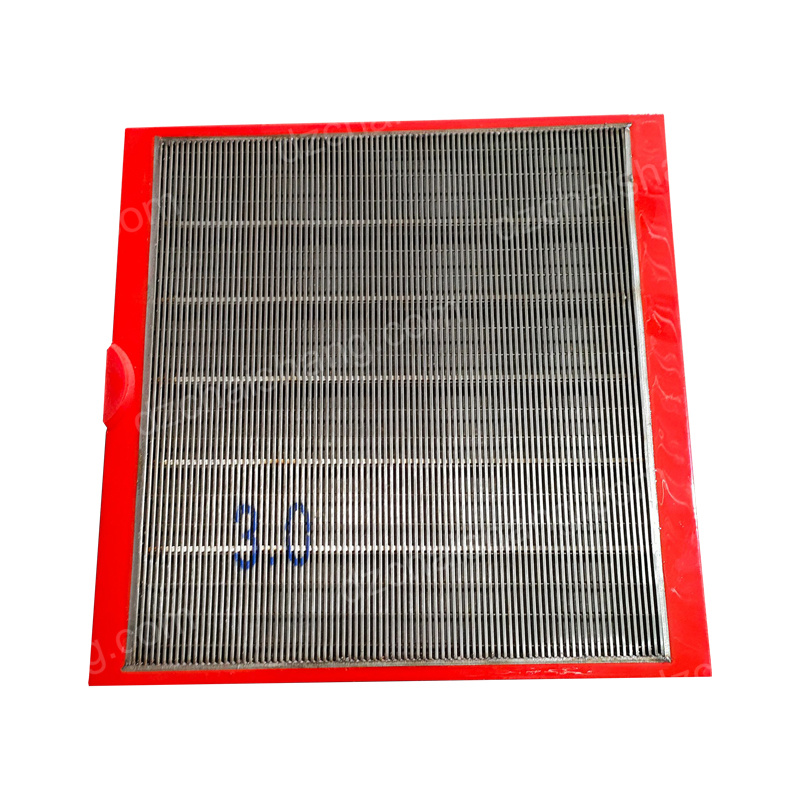
ভিব্রেটিং স্ক্রিনগুলি বিভিন্নশিল্প প্রক্রিয়ায়অপরিহার্য, বিশেষকরেখনিজ, রাসায়নিক এবং সমষ্টির মতো উপকরণ পরিচালনার ক্ষেত্রে।এই স্ক্রিনগুলিকম্পনের মাধ্যমে বিভিন্ন আকারের কণাকে আলাদা করার জন্য ডিজাইন করা হয়েছে,সহজ হ্যান্ডলিংএবং প্রক্রিয়াকরণের সুবিধার্থে।কম্পনশীল পর্দার কার্যক্ষমতাএবং দীর্ঘায়ুকে উল্লেখযোগ্যভাবে প্রভাবিত করে এমন উপাদানগুলিরমধ্যে রয়েছে টেনশন ডেক। ঐতিহ্যগতভাবেইস্পাতবা তারের জালের মতো উপকরণ থেকে তৈরি,এই ডেকগুলি উপকরণগুলিরসঠিক গ্রেডিং এবং বাছাইয়ের জন্য গুরুত্বপূর্ণ। যাইহোক,সাম্প্রতিক উদ্ভাবনগুলিদেখেছে পলিউরেথেন এবং রাবার তাদের স্থায়িত্ব এবং দক্ষতার কারণে জনপ্রিয় পছন্দ হয়ে উঠেছে। প্রাথমিক সুবিধাগুলির মধ্যে একটি হল তাদের ঘর্ষণ এবং পরিধানের উচ্চ প্রতিরোধ।একটি স্পন্দিত স্ক্রিনের চাহিদাপূর্ণপরিবেশে, যেখানে উপাদান ক্রমাগত পৃষ্ঠকে প্রভাবিতকরে, পরিধানের প্রতিরোধ স্ক্রিনডেকের কার্যক্ষমজীবনকে প্রসারিতকরে।এই স্থায়িত্ব স্ক্রীনিং প্রক্রিয়ার সামঞ্জস্য বজায় রাখতেও সাহায্য করে, নিশ্চিত করে যে উপাদানের আকার দীর্ঘ সময়ের জন্য সমান থাকে,এইভাবে প্রতিস্থাপনএবং রক্ষণাবেক্ষণের জন্য ডাউনটাইমহ্রাসকরে। স্পন্দিত স্ক্রিনগুলি উল্লেখযোগ্যপরিমাণে শব্দ তৈরি করতে পারে,যা শুধুমাত্র একটি উপদ্রবই নয় কিন্তু শিল্প সেটিংসে শ্রমিকদের জন্য গুরুতর স্বাস্থ্য ঝুঁকিও তৈরি করতে পারে। রাবার এবং পলিউরেথেনের অন্তর্নিহিত গুণ রয়েছে যা ধাতুর চেয়ে ভাল কম্পন শোষণ করে,যার ফলে শব্দের মাত্রা উল্লেখযোগ্যভাবে হ্রাস পায়। এটি শুধুমাত্র একটি ভাল কাজের পরিবেশে অবদান রাখে না বরং শব্দ দূষণ সংক্রান্ত ক্রমবর্ধমান কঠোর কর্মক্ষেত্রের নিয়ম মেনে চলতে সহায়তা করে। ধাতুর বিপরীতে, পলিউরেথেন এবং রাবার মরিচা বা ক্ষয় করে না,যা ভিজা বা ক্ষয়কারী উপাদান যুক্ত অ্যাপ্লিকেশনগুলিতে বিশেষভাবেউপকারী।এই বৈশিষ্ট্যটিনিশ্চিত করে যে ভাইব্রেটিং স্ক্রিনের টেনশন ডেকের কাঠামোগত অখণ্ডতাবজায় রাখাহয়েছে,অকাল ব্যর্থতাএবংসম্ভাব্য নিরাপত্তা ঝুঁকি প্রতিরোধকরে।
পলিউরেথেন এবং রাবারের কাস্টমাইজেশনসম্ভাবনাও একটি উল্লেখযোগ্য সুবিধা।এইউপকরণগুলি নির্দিষ্ট অ্যাপ্লিকেশনএবং স্ক্রিন ডিজাইনের সাথে মানানসইকরারজন্য বিভিন্ন আকার এবং আকারে তৈরি করা যেতে পারে। এই নমনীয়তা এমন ডিজাইনের মাধ্যমে পর্দার কার্যকারিতা অপ্টিমাইজ করার অনুমতি দেয় যা ভাল উপাদান প্রবাহকে উন্নীত করে এবং অন্ধ হওয়া এবং পেগিংপ্রতিরোধকরে,যা ঐতিহ্যগত স্ক্রিনডেকের সাথে সাধারণ সমস্যা। এই ধরনের উদ্ভাবনগুলি অরিজিনালইকুইপমেন্ট ম্যানুফ্যাকচারারদের(OEM) জন্য অত্যন্ত গুরুত্বপূর্ণযারা ক্রমাগততাদের গ্রাহকদের আরও ভাল মূল্য এবং কর্মক্ষমতা প্রদানের জন্য তাদের পণ্যগুলিকে উন্নত করতে চায়। এবং বিভিন্ন শিল্পে সাশ্রয়ী মূল্যেরউপাদান হ্যান্ডলিং। প্রযুক্তিরউন্নতির সাথে সাথে,এই উপকরণগুলি আরও পরিশীলিত হয়ে উঠছে, তাদের বৈশিষ্ট্যগুলিকে আরও উন্নত করার জন্য তাদের গঠনের উন্নতির সাথে। OEM এই উদ্ভাবনের অগ্রভাগে রয়েছে,রাবার এবং পলিউরেথেন টেনশন ডেকগুলিরবিকাশএবং পরিমার্জন যা তাদের গ্রাহকদের নির্দিষ্ট চাহিদা পূরণ করে,নিশ্চিত করে যে স্ক্রিনগুলি সর্বোচ্চ দক্ষতায় কাজ করে এবং তারা যে শিল্প প্রক্রিয়াগুলিরঅংশ সেগুলির সামগ্রিক উত্পাদনশীলতায় অবদান রাখে৷
উপসংহারে,স্পন্দিত পর্দায় রাবার এবং পলিউরেথেন টেনশন ডেকের দিকে অগ্রসর হওয়া শিল্পের প্রতিফলন উদ্ভাবনযাদক্ষতা, নিরাপত্তা এবং পরিবেশগত স্টুয়ার্ডশিপপূরণ করে।এইউপকরণগুলি স্পন্দিত স্ক্রীনগুলির কার্যকারিতার মানগুলিকেপুনরায় সংজ্ঞায়িত করার জন্য সেট করা হয়েছে,যা শিল্প সরঞ্জামগুলির ল্যান্ডস্কেপেএগুলিকে অপরিহার্য করে তোলে৷
用于 OEM 振动筛应用的橡胶张力板的创新
振动筛在各种工业过程中至关重要,特别是在矿物、化学品和骨料等材料的处理中。这些筛子旨在通过振动分离不同尺寸的颗粒,从而更容易处理和加工。张力板是对振动筛的效率和寿命产生显着影响的部件之一。这些甲板传统上由钢或丝网等材料制成,对于材料的正确分级和分类至关重要。然而,最近的创新使聚氨酯和橡胶因其耐用性和效率而成为流行的选择。
聚氨酯和橡胶张力板比传统同类产品具有明显的优势。主要优点之一是其高耐磨性。在振动筛的严苛环境中,材料不断冲击表面,耐磨性可以延长筛板的使用寿命。这种耐用性还有助于保持筛选过程的一致性,确保材料尺寸在较长时间内保持均匀,从而减少更换和维护的停机时间。
使用橡胶和聚氨酯的另一个优点是它们的降噪特性。振动筛会产生大量噪音,这不仅令人烦恼,而且还会对工业环境中的工人造成严重的健康风险。橡胶和聚氨酯具有比金属更好的吸收振动的固有品质,从而显着降低噪音水平。这不仅有助于创造更好的工作环境,还有助于遵守有关噪音污染的日益严格的工作场所法规。
此外,这些材料具有出色的耐湿气和加工材料的化学性质引起的腐蚀能力。与金属不同,聚氨酯和橡胶不会生锈或腐蚀,这在涉及潮湿或腐蚀性材料的应用中特别有益。此功能可确保保持振动筛张力板的结构完整性,防止过早失效和潜在的安全隐患。
聚氨酯和橡胶的定制潜力也是一个显着优势。这些材料可以模制成各种形状和尺寸,以适应特定的应用和屏幕设计。这种灵活性可以通过促进更好的物料流动并防止堵塞和堵塞的设计来优化筛网性能,这是传统筛板的常见问题。这些创新对于原始设备制造商 (OEM) 来说至关重要,他们不断寻求改进产品,为客户提供更好的价值和性能。
在振动筛中采用聚氨酯和橡胶张力板代表着向更高效、更安全、更高效的方向的重大转变。以及各个行业中具有成本效益的物料搬运。随着技术的进步,这些材料变得越来越复杂,其配方得到改进,进一步增强了其性能。 OEM 处于这一创新的前沿,开发和精炼橡胶和聚氨酯张力板,满足客户的特定需求,确保筛网以最高效率运行,并为其所属工业流程的整体生产力做出贡献。
总而言之,振动筛转向橡胶和聚氨酯张力板反映了该行业追求效率、安全和环境管理创新的动力。这些材料将重新定义振动筛的性能标准,使其在工业设备领域不可或缺。