筛板,PU筛板,聚氨酯筛板
مزاياألواحشاشة البولي يوريثينفي تطبيقات الغربلةعالية التآكل
في عالم تطبيقات الغربلةعاليةالتآكل، يستمر البحث عن المواد التي يمكنهاتحمل المتطلبات الصارمة للفرزوالغربلةوالفصل دونالخضوعللتآكل السريع。 منبينعددلايحصىمن الخيارات المتاحة للصناعات، برزت ألواح شاشات البولي يوريثين باعتبارهاالمرشح الأوفر حظًا، حيث توفر مزيجًامنالمتانة والكفاءةوالتنوعالذي يصعبمطابقته。 تتعمقهذهالمقالةفي مزاياألواحشاشة البولي يوريثين، وتسلط الضوءعلىسببتحولها بشكلمتزايدإلىالمادة المفضلةلتطبيقات الفحصعالية التآكل。
البولي يوريثين، أو PU، عبارة عن مادةاصطناعيةمعروفة بمرونتهاالاستثنائية وقوتهاومقاومتها للعواملالجوية。 التآكلوالتمزقوالماء。 هذه الصفات المتأصلة تجعل لوحات شاشة PU مناسبة بشكلخاصلتطبيقات الفحص حيث تكون المواد كاشطةأومبللةأو كليهما。 على عكس مواد الغربلة التقليديةمثلالشبكات السلكية، والتي يمكن أن تتآكلبسرعةوتتطلب استبدالات متكررة، فإن ألواح شاشات البولي يوريثينتوفرطولالعمر الذي يترجم إلى توفير في التكاليفوتقليلوقت التوقفعنالعمل للصيانة。
إحدىالمزايا الأساسيةلألواحشاشات البولي يوريثينهي تفوقهامقاومةالتآكل。 تسمح قوة الشد والمرونة العاليةللمادة بامتصاصالصدمات ومقاومةنوعالتآكل الذي يؤدي عادةً إلى تقصيرعمرموادالفحص الأخرى。 لاتعملهذهالمرونةعلى إطالةعمرخدمةلوحات الشاشةفحسب،بلتحافظ أيضًاعلىكفاءةالفحص بمرورالوقت،ممايضمن التوزيعالمتسقلحجم الجسيمات والإنتاجية。
علاوةعلى ذلك، تم تصميم لوحات الشاشةالمصنوعةمن مادةالبولييوريثينمع أخذالمرونةفي الاعتبار، ممايسمح بتخصيصهالتناسب مجموعةواسعةمنمعدات الفحصوالتطبيقات。 سواء كان المطلبيتعلق بالغربلةالناعمةأو الخشنة، أو الظروف الرطبةأوالجافة،يمكن PU بأشكالوأحجام وتكويناتمختلفة لتلبيةالاحتياجات التشغيليةالمحددة。 يتمتعزيزهذهالقدرة علىالتكيفبشكلأكبرمن خلالقدرةالمادةعلى تقليلالضوضاء والاهتزازأثناء التشغيل،ممايساهمفي بيئةعملأكثرأمانًا وممتعة。
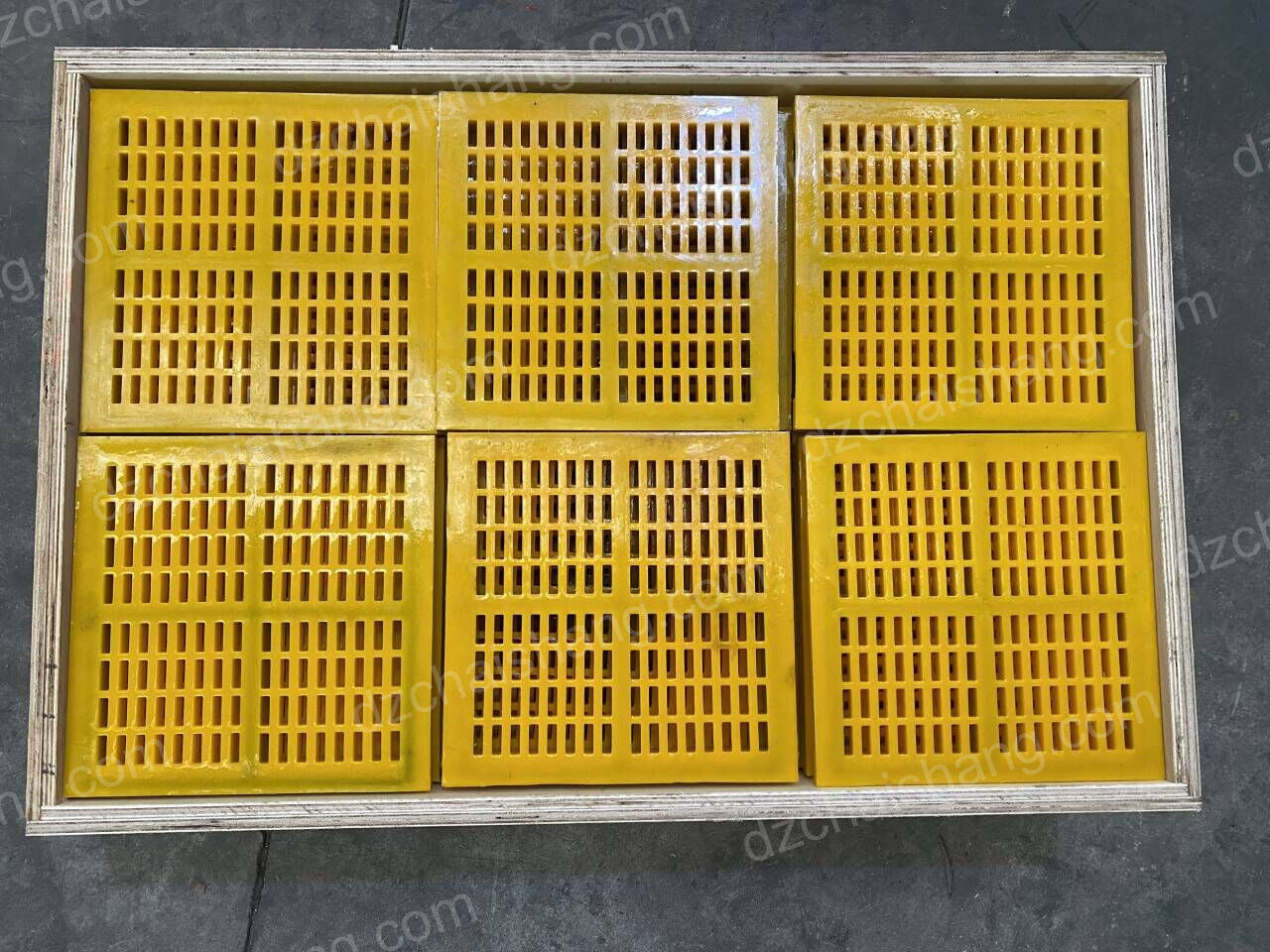
الابتكارات في تصميم لوحة شاشة PU لتحسين فصل المواد ومتانتها
شهد عالم فصل المواد وغربلتهاتطوراتكبيرة معتقديملوحاتشاشة البولييوريثين(PU)。 أحدثت هذهالألواح المبتكرةثورةفي الطريقةالتيتتعامل بهاالصناعاتمععملية الفصل، حيث تقدم مزيجًا منالأداءالعالي والمتانةالتيتتفوق علىموادالفحص التقليديةمثلالشبكات السلكيةوالفولاذ。 نظرًالأنالصناعات تسعىباستمرارإلىطرق أكثركفاءةوفعاليةمن حيث التكلفةلمعالجة المواد، فإن تطور تصميم لوحة شاشة PU يبرز كتطور رئيسي في تلبيةهذه المطالب。
تشتهرألواح شاشة البولي يوريثين بمقاومتها الاستثنائيةللتآكل وقدرتهاعلىتحمل الظروفالقاسية。 شروط。 ترجعهذهالمرونةإلى الخصائصالفريدة للبولي يوريثين، وهو بوليمرمتعدد الاستخداماتيمكن هندستهلتحقيقنطاق واسعمنالصلابة والمرونة。 ونتيجةلذلك،تكون ألواح شاشة PU أقل عرضة للتآكل، مما يترجم إلى عمرخدمةأطولوتقليل وقت التوقف عن العمل للصيانة。 تعد هذه المتانة مفيدة بشكل خاص في صناعات مثل التعدينواستغلال المحاجرومعالجة الركام، حيث تتعرض المعدات بانتظام للأحمالالثقيلة والمواد الكاشطة.
علاوة على ذلك، تسمح مرونة تصميمالبولييوريثين بالتخصيصليناسب تطبيقاتغربلةمحددة。 يمكنللمصنعينتخصيص حجم وشكل ونمط فتحات الشاشةلتحسينعملية الفصلللموادالمختلفة。 تضمن إمكانيةالتخصيص PU يمكنهاالتعاملبكفاءة معمجموعةمتنوعةمن المواد، بدءًامن الرمالالناعمةوحتى الصخورالكبيرة،مع الحفاظعلىالدقةفي الفصل。 تعد دقة فصل المواد أمرًابالغالأهميةفي تحقيقجودةالمنتج المطلوبةوفيتقليلهدر الموارد القيمة.
أحد الابتكاراتالمهمة الأخرى في تصميم لوحة شاشة PU هو تطوير الأنظمة المعيارية。 تتميزهذهالأنظمة بلوحات فرديةيمكن استبدالهاأوإعادة تشكيلهابسهولة،مما يوفر للمشغلينالمرونة اللازمةللتكيفمع متطلبات الفحص المتغيرةدونالحاجة إلىاستبدالأسطح الشاشةبأكملها。 يعملالتصميمالمعياري أيضًاعلىتبسيطأعمال الصيانةوالإصلاح،حيث يمكنتبديلالألواح الباليةأوالتالفة بسرعة، مما يقلل من الاضطراباتفيعملية الغربلة。
يعد التأثيرالبيئي لعمليات الغربلةأحد الاعتبارات ذات الأهميةالمتزايدة، وتساهم لوحات شاشة PU بشكل إيجابي في هذا الصدد 。 ويعني طول عمرها أنها تحتاج إلى الاستبدال بشكلأقلتكرارًامن مواد الفحص الأخرى، مما يؤدي إلى تقليل النفايات。 بالإضافةإلىذلك،فإن الطاقةالمطلوبة لإنتاج مادة البولي يوريثينأقلبشكلعاممن تلكالمستخدمةفي الشاشات المعدنية، مما يقللبشكلأكبرمن البصمةالكربونية لعملياتالغربلة。
منحيثالأداء،توفر لوحات شاشة PU تقليلًا فائقًاللضوضاءمقارنة بالشاشاتالمعدنية。 تساهمخصائصتخميد الصوت المتأصلة في مادة البولي يوريثين في خلق بيئةعملأكثرهدوءًا، وهو أمر مفيد لكل من القوىالعاملة والامتثالللوائح الضوضاء。 تعتبرهذهالميزةمفيدة بشكلخاصفيالمناطق الحضريةأوالسكنيةحيث يمكنأنيكونالتلوث الضوضائي مصدر قلق كبير。
يستمر البحث والتطوير المستمرفيتقنيةلوحة شاشة PU في دفع حدود ما هو ممكنفيفصلالمواد。 ويجري استكشاف ابتكارات مثلالأسطح المضادةللعمى والهياكلالمعززة لزيادةتعزيزكفاءة وموثوقيةهذهالألواح。 معتحركالصناعةنحو ممارسات أكثر استدامة وفعاليةمنحيث التكلفة،منالمقررأن PU أكثرتكاملاً。
في الختام، تمثلالتطورات في تصميم لوحة شاشة PU قفزة كبيرةإلىالأمامفي مجالفصلالمواد 。 بفضلمتانتهاالتيلا مثيللها،وميزاتها القابلةللتخصيص، وفوائدهاالبيئية،تضع هذهاللوحاتمعايير جديدةللكفاءةوالأداء。 نظرًالأنالصناعاتفي جميع أنحاء العالم تسعى جاهدةلتحسين عملياتها، فإن اعتماد حلولفحصالبولي يوريثينيعدخيارًا واضحًالأولئكالذين يتطلعونإلىالبقاءفي المقدمةفيمشهدتنافسي。
用于增强材料分离和耐用性的 PU 筛板设计创新
随着聚氨酯 (PU) 筛板的引入,材料分离和筛分领域取得了显着进步。这些创新面板彻底改变了行业处理分离过程的方式,提供超越金属丝网和钢材等传统筛分材料的高性能和耐用性。随着各行业不断寻求更高效、更具成本效益的材料加工方法,PU 筛板设计的发展成为满足这些需求的关键发展。
聚氨酯筛板以其卓越的耐磨性和承受恶劣环境的能力而闻名。状况。这种弹性归功于聚氨酯的独特性能,聚氨酯是一种多功能聚合物,经过设计可实现广泛的硬度和弹性。因此,PU 筛板不易磨损,从而延长了使用寿命并减少了维护停机时间。这种耐用性对于采矿、采石和骨料加工等行业尤其有利,这些行业的设备经常暴露在重负载和磨料下。
此外,聚氨酯的设计灵活性允许进行定制,以适应特定的筛分应用。制造商可以定制筛孔的尺寸、形状和图案,以优化不同材料的分离过程。这种定制能力确保 PU 筛板能够有效处理从细沙到大岩石的各种物质,同时保持分离的准确性。材料分离的精度对于实现所需的产品质量和最大限度地减少宝贵资源的浪费至关重要。
PU 筛板设计的另一项重大创新是模块化系统的开发。这些系统具有可轻松更换或重新配置的单独面板,使操作员能够灵活地适应不断变化的筛分要求,而无需更换整个筛板。模块化设计还简化了维护和修理,因为磨损或损坏的面板可以快速更换,从而最大限度地减少对筛选过程的干扰。筛选操作对环境的影响是一个越来越重要的考虑因素,而 PU 筛选面板在这方面做出了积极贡献。它们的使用寿命长意味着它们比其他筛分材料需要更换的频率更低,从而减少了浪费。此外,生产聚氨酯所需的能源通常低于金属筛网,进一步减少了筛分操作的碳足迹。
在性能方面,与金属筛网相比,PU筛板具有卓越的降噪性能。聚氨酯固有的隔音特性有助于营造更安静的工作环境,这对员工和遵守噪音法规都有好处。此功能在噪声污染可能成为严重问题的城市或住宅区尤其有利。
PU 筛板技术的持续研究和开发不断突破材料分离的可能性界限。正在探索防盲表面和加固结构等创新,以进一步提高这些面板的效率和可靠性。随着行业朝着更加可持续和更具成本效益的方向发展,PU 筛板的作用将变得更加不可或缺。
总而言之,PU 筛板设计的进步代表了材料分离领域的重大飞跃。凭借其无与伦比的耐用性、可定制功能和环境效益,这些面板正在为效率和性能树立新的标准。随着世界各地的行业努力优化其运营,对于那些希望在竞争格局中保持领先地位的企业来说,采用聚氨酯筛选解决方案是一个明智的选择。