Bảng màn hình polyurethane, lưới màn hình polyurethane
فوائد استخدام لوحات شاشة البولي يوريثان في عمليات التعدين
كيفية صيانة وتنظيف شبكة شاشة البولي يوريثان بشكل صحيح
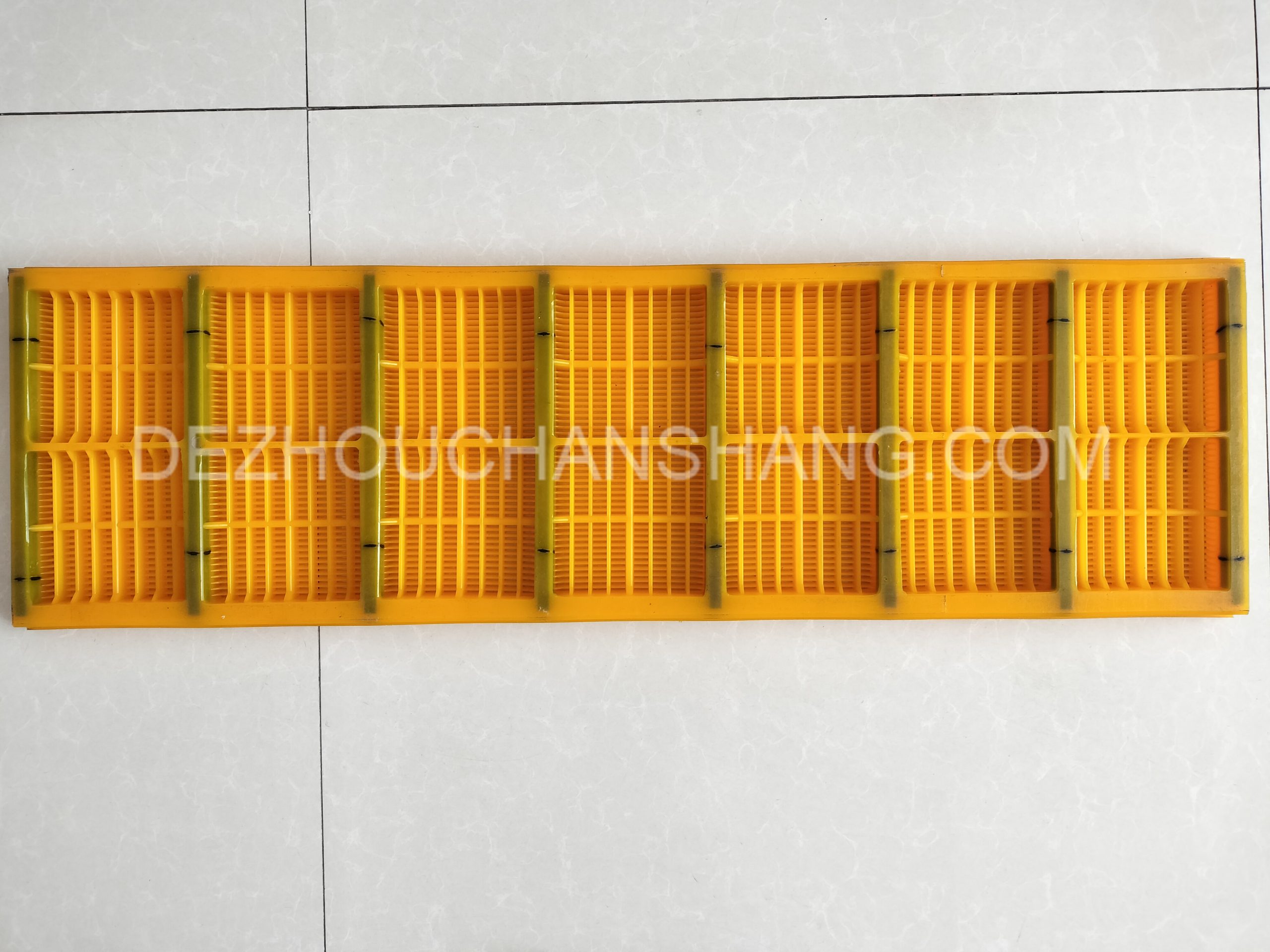
لوحات شاشة البولي يوريثان هي خيار شائع للعديد من الصناعات بسبب متانتها وكفاءتها في فصل المواد. ومع ذلك ، مثل أي معدات أخرى ، فإنها تتطلب الصيانة والتنظيف المناسبين لضمان الأداء الأمثل وطول العمر. في هذه المقالة ، سنناقش كيفية الحفاظ بشكل صحيح على شبكة شاشة البولي يوريثان وتنظيفها لزيادة فعاليتها إلى الحد الأقصى. من الضروري التحقق من أي علامات للبلى ، مثل الدموع أو الثقوب أو الحواف الفضفاضة. يمكن أن تؤدي هذه المشكلات إلى انخفاض الكفاءة وقد تتطلب اهتمامًا فوريًا لمنع مزيد من الضرر. من خلال إجراء عمليات التفتيش الروتينية ، يمكنك تحديد أي مشاكل في وقت مبكر ومعالجتها قبل التصاعد.
بالإضافة إلى عمليات التفتيش المرئية ، من الأهمية بمكان مراقبة توتر لوحات الشاشة. بمرور الوقت ، يمكن أن يخفف التوتر ، مما يؤثر على عملية الفحص. للحفاظ على التوتر الأمثل ، يوصى بضبط التوتر بانتظام باستخدام الأدوات المناسبة. سيساعد هذا على ضمان محاذاة لوحات الشاشة وتعمل بشكل صحيح على النحو المقصود.
جانب آخر مهم في الحفاظ على شبكة شاشة البولي يوريثان هو التنظيف. يعد التنظيف المنتظم ضروريًا لمنع تراكم المواد ، والذي يمكن أن يسد الشاشة ويقلل من فعاليتها. لتنظيف لوحات الشاشة ، ابدأ بإزالة أي مادة زائدة باستخدام فرشاة أو ضاغط الهواء. بعد ذلك ، استخدم محلول منظف معتدل وماء لتنظيف سطح لوحات الشاشة برفق. تجنب استخدام المواد الكيميائية القاسية أو المواد الكاشطة ، حيث يمكن أن تلحق الضرر بمواد البولي يوريثان. السماح للألواح أن تجف تمامًا قبل إعادة تثبيتها. يوصى أيضًا بتطبيق طبقة واقية أو مواد تشحيم على لوحات الشاشة لمنع البلى المبكرة. تجنب استخدام كائنات حادة أو قوة مفرطة عند التعامل مع اللوحات ، لأن هذا يمكن أن يسبب الدموع أو الثقوب. قم بتخزين الألواح في منطقة نظيفة وجافة بعيدًا عن أشعة الشمس المباشرة ودرجات الحرارة القصوى لإطالة عمرها. من خلال إجراء عمليات التفتيش الروتينية ، ومراقبة التوتر ، وتنظيف اللوحات بانتظام ، يمكنك التأكد من أداء الجهاز الخاص بك في أفضل حالاته. تذكر أن تتعامل مع الألواح بعناية وتخزينها بشكل صحيح لمنع الضرر. مع الصيانة المناسبة ، ستستمر لوحات شاشة البولي يوريثان في توفير فحص موثوق به لسنوات قادمة.
পলিউরেথেন স্ক্রিন প্যানেলগুলি বিভিন্ন শিল্পের জন্য তাদের স্থায়িত্ব এবং পৃথক করার ক্ষেত্রে দক্ষতার কারণে একটি জনপ্রিয় পছন্দ। তবে অন্য যে কোনও সরঞ্জামের মতো, তাদের সর্বোত্তম কর্মক্ষমতা এবং দীর্ঘায়ু নিশ্চিত করার জন্য তাদের যথাযথ রক্ষণাবেক্ষণ এবং পরিষ্কার করা প্রয়োজন। এই নিবন্ধে, আমরা এর কার্যকারিতা সর্বাধিকতর করার জন্য কীভাবে পলিউরেথেন স্ক্রিন জালটি সঠিকভাবে বজায় রাখতে এবং পরিষ্কার করতে পারি তা নিয়ে আলোচনা করব
পলিউরেথেন স্ক্রিন প্যানেলগুলি বজায় রাখার অন্যতম গুরুত্বপূর্ণ দিক নিয়মিত পরিদর্শন। অশ্রু, গর্ত বা আলগা প্রান্তের মতো পরিধান এবং টিয়ার কোনও লক্ষণ পরীক্ষা করা অপরিহার্য। এই সমস্যাগুলি দক্ষতা হ্রাস করতে পারে এবং আরও ক্ষতি রোধে তাত্ক্ষণিক মনোযোগের প্রয়োজন হতে পারে। রুটিন পরিদর্শন পরিচালনা করে, আপনি যে কোনও সমস্যা প্রথম দিকে সনাক্ত করতে পারেন এবং সেগুলি বাড়ানোর আগে তাদের সম্বোধন করতে পারেন
ভিজ্যুয়াল পরিদর্শন ছাড়াও, স্ক্রিন প্যানেলগুলির উত্তেজনা নিরীক্ষণ করাও গুরুত্বপূর্ণ। সময়ের সাথে সাথে, উত্তেজনা আলগা করতে পারে, স্ক্রিনিং প্রক্রিয়াটিকে প্রভাবিত করে। সর্বোত্তম উত্তেজনা বজায় রাখতে, উপযুক্ত সরঞ্জামগুলি ব্যবহার করে নিয়মিত উত্তেজনা সামঞ্জস্য করার পরামর্শ দেওয়া হয়। এটি নিশ্চিত করতে সহায়তা করবে যে স্ক্রিন প্যানেলগুলি যথাযথভাবে সারিবদ্ধ এবং উদ্দেশ্য হিসাবে কাজ করছে
পরিষ্কার করার পরে, কোনও অবশিষ্টাংশ অপসারণের জন্য পরিষ্কার জল দিয়ে স্ক্রিন প্যানেলগুলি ভালভাবে ধুয়ে ফেলুন। প্যানেলগুলি পুনরায় ইনস্টল করার আগে পুরোপুরি শুকানোর অনুমতি দিন। অকাল পরিধান এবং টিয়ার প্রতিরোধের জন্য স্ক্রিন প্যানেলগুলিতে একটি প্রতিরক্ষামূলক লেপ বা লুব্রিক্যান্ট প্রয়োগ করার পরামর্শ দেওয়া হয়
নিয়মিত রক্ষণাবেক্ষণ এবং পরিষ্কার করার পাশাপাশি ক্ষতি রোধে যত্ন সহ পলিউরেথেন স্ক্রিন প্যানেলগুলি পরিচালনা করা অপরিহার্য। প্যানেলগুলি পরিচালনা করার সময় তীক্ষ্ণ বস্তু বা অতিরিক্ত শক্তি ব্যবহার করা এড়িয়ে চলুন, কারণ এটি অশ্রু বা পাঙ্কচারের কারণ হতে পারে। তাদের জীবনকাল দীর্ঘায়িত করার জন্য সরাসরি সূর্যের আলো এবং চরম তাপমাত্রা থেকে দূরে একটি পরিষ্কার, শুকনো অঞ্চলে প্যানেলগুলি সংরক্ষণ করুন
নিয়মিত পরিদর্শন পরিচালনা, উত্তেজনা পর্যবেক্ষণ এবং নিয়মিত প্যানেলগুলি পরিষ্কার করে আপনি নিশ্চিত করতে পারেন যে আপনার সরঞ্জামগুলি সর্বোত্তমভাবে সম্পাদন করে। যত্ন সহ প্যানেলগুলি পরিচালনা করতে ভুলবেন না এবং ক্ষতি রোধ করতে সেগুলি সঠিকভাবে সঞ্চয় করুন। যথাযথ রক্ষণাবেক্ষণের সাথে, আপনার পলিউরেথেন স্ক্রিন প্যানেলগুলি আগামী কয়েক বছর ধরে নির্ভরযোগ্য স্ক্রিনিং সরবরাহ করতে থাকবে