聚氨酯筛网、聚氨酯筛板、聚氨酯筛网
مزايافحصالبولي يوريثانفيعمليات التعدينالحديثة
نصائح التثبيت والصيانةلألواحشاشة PU
العنوان:نصائحالتثبيت والصيانةلألواحشاشة PU
أصبحت حلول غربلة البولي يوريثين، المعروفةعمومًا بألواح شاشة PU أو شبكات البولي يوريثين،شائعة بشكلمتزايدفي التطبيقات الصناعية المختلفةنظرًا لمتانتهاالاستثنائية ومرونتهاوكفاءتهافي فصلالموادوغربلتها。 تُستخدمهذهالألواح علىنطاقواسعفي التعدينومعالجة الركاموالصناعات الأخرىالتيتكونفيها عمليات الفحصبالغة الأهمية。 لضمانأداءهذهاللوحات علىالنحوالأمثل،يعد التثبيت والصيانة المناسبةأمرًا ضروريًا。 توفرهذهالمقالةرؤى قيمةحولأفضل الممارسات لتثبيت PU لزيادةعمرها الافتراضي وفعاليتها إلى أقصى حد.
عند التحضير لتركيبلوحاتشاشة PU،من الضروري البدء بإجراء فحص شامل لإطار الغربلة أوسطحها 。 يجبأنيكونالهيكل خاليًامنأيضررأوحطام أومخالفاتقدتؤثرعلى ملاءمةاللوحةأو أدائها。 يعد ضمان سطح نظيف ومستوي الخطوةالأولى نحوالتثبيتالناجح。 بالإضافةإلىذلك،من المهمالتحققمنأن قضبانالدعمفيحالة جيدةومحاذاتهابشكل صحيح، لأنها تلعب دورًا محوريًافيدعمالألواح وتوزيعالحمل بالتساوي。
بمجردأنيصبح إطار الغربلةجاهزًا، يتم تركيب شبكة البولي يوريثينيمكنأنتبدأ。 وينبغي الحرصعلى محاذاةاللوحاتبشكل صحيح، باتباع إرشادات الشركةالمصنعة。 لايمكنالمبالغةفيدقة هذهالخطوة،حيثأن المحاذاةغيرالصحيحة يمكن أن تؤدي إلى التآكل المبكر، وانخفاضكفاءة الفحص، والضررالمحتمل للألواحأوالجهاز。 يعد تثبيت الألواح بشكل آمنأمرًاحيويًاأيضًا。 اعتمادًاعلىالتصميم، قد يتضمن ذلك التثبيت أو التثبيتأوالطرق الأخرىالتيتوفرها الشركةالمصنعةللوحة。 منالضروريالتأكدمن تشديد جميع أدوات التثبيت وفقًا للمواصفات الموصىبها لمنع أي حركة أثناء التشغيل。
بالانتقالإلى الصيانة، يتأثر طولعمر وأداء لوحات شاشة PU بشكل كبيربالرعاية المنتظمةوالسليمة。 يجب إجراء عمليات فحص روتينيةلتحديدأي علامات تآكل، مثل الثقوبأوالتمزقاتأو السحجات。 يسمح الاكتشافالمبكر لهذهالمشكلاتبإجراء الإصلاحات أو الاستبدالاتفيالوقت المناسب، وبالتالي تجنبالتوقفغير المتوقعوالأضرار المحتملةللمكونات الأخرىلمعداتالفحص。 يعدتنظيفالألواح جانبًامهمًاآخرمن جوانبالصيانة。 يمكن أن يؤدي تراكم المواد على الشاشة إلى إعاقةكفاءةالفحص ويؤدي إلى زيادة الضغط علىالألواح。 سيساعد التنظيفاللطيف باستخدامالأدوات والحلولالمناسبة الموصىبهامنقبل الشركةالمصنعةفي الحفاظعلىسلامةمادة البولي يوريثين。
علاوةعلىذلك،يُنصح بمراقبةتشغيلمعدات الفحصعنكثب。 يمكنأنتشيرالضوضاءأو الاهتزازات أو التغييرات غير المعتادةفيالأداءإلى وجود مشكلات في لوحات شاشة PUأوالجهازنفسه。 معالجةهذهالحالات الشاذةعلىالفوريمكن أنتمنعالمزيدمن المضاعفات。 منالمفيدأيضًا الاحتفاظبمخزونمن اللوحات البديلة والمثبتاتفيمتناول اليد لتقليل وقت التوقف عنالعملفيحالةتعطل اللوحة。
في الختام، تعتمدفعاليةفحص البولي يوريثينفي التطبيقات الصناعية علىالتثبيتالصحيح والصيانةالدؤوبة。 منخلالالتأكدمنأن إطارالغربلةفيحالة مثالية، ومحاذاة الألواح وتأمينهابشكل صحيح، وإجراءعمليات فحصمنتظمة،والحفاظ علىالنظافة،يمكن إطالةعمرخدمةألواح الشاشة PUبشكلكبير。 لاتعملهذهالممارسات علىحمايةالاستثمارفي شبكات البولي يوريثين فحسب، بل تساهم أيضًا في الإنتاجيةالشاملة وكفاءةعملياتالفحص。 معوضعهذهالنصائحفي الاعتبار،يمكن للمشغلينأنيتوقعوا أداءً موثوقًامنلوحات شاشات PU الخاصة بهم، مما يؤدي في النهايةإلى نتائج محسنة لعمليات الفحصالخاصة بهم.
مقارنةشبكةالبولي يوريثينبموادالغربلة التقليدية
لقد ظهر فحص البولي يوريثين، والذي يشار PU أوشبكةالبولي يوريثين، كتقدم كبير في مجالفصلالمواد وتصنيفها。 يوفرحلالغربلة المبتكرهذامجموعة كبيرةمنالمزايا مقارنةبموادالفحص التقليدية،مثل الشبكات السلكية والشاشات المطاطية، ممايجعلهخيارًا مفضلاً لمختلف التطبيقاتالصناعية。 تكشفالمقارنةبين شبكات البولي يوريثين ومواد الفحص التقليدية عنفهمشامللخصائصها المميزةوفوائدهاومدى ملاءمتهالظروف التشغيلالمختلفة。
تشتهرشبكةالبولي يوريثينبمتانتها الاستثنائية ومقاومتهاللتآكل。 ويرجعذلكفيالمقام الأولإلىالخصائص الكامنةفيمادةالبولي يوريثين،وهوبوليمر متعدد الاستخدامات يجمعبينمرونةالمطاط وصلابةالمعدنومتانته。 على عكس شاشات الشبكات السلكيةالتقليدية، التي يمكن أن تستسلم بسهولةللتآكل والتآكل، فإنشاشات البولي يوريثينتتحمل المواد والبيئات القاسية،ممايطيلعمر الخدمةبشكلكبير。 لاتقللهذهالمتانةمن الحاجةإلىعمليات استبدالمتكررةفحسب، بلتقللأيضًامنوقت التوقفعنالعمل،مما يعززالكفاءة التشغيلية。
علاوةعلىذلك،يُظهر غربالالبولييوريثين مقاومةفائقةللعوامل البيئيةالمختلفة،بما فيذلكالرطوبةوالأشعة فوقالبنفسجيةوتقلبات درجاتالحرارة。 غالبًاماتتحللالمواد التقليديةمثلالمطاط والشبكات السلكيةفيظل الظروفالقاسية،مما يؤدي إلى فقدان السلامة الهيكليةوالأداء。 في المقابل، تحافظ لوحات شاشة PU على خصائصها الفيزيائيةووظائفها، مما يضمن أداءً ثابتًا بغضالنظرعنبيئة التشغيل。 هذهالمرونةتجعلشبكة البولي يوريثينخيارًا مثاليًاللتطبيقات الخارجيةوالصناعات التي تتعامل مع المواد المسببةللتآكل.
ميزة أخرىملحوظةلشبكة البولي يوريثينهي مرونتهاوخيارات التخصيص。 يمكن تشكيل مادة البولي يوريثينفيمجموعة واسعةمنالأشكال والأحجاموالتكوينات، ممايسمحبحلولمخصصة تلبي متطلبات الفحص المحددة。 تعد هذه القدرة على التكيفمفيدةبشكلخاص فيالتطبيقاتالتي تتطلبفصلًادقيقًا للجسيماتوتصنيفًا للحجم。 منناحيةأخرى،توفر مواد الفحص التقليدية خيارات تخصيصمحدودة، ممايستلزمفيكثيرمن الأحيانالتنازلاتفي الكفاءة والفعالية.
تتفوقشاشات البولي يوريثينأيضًا منحيثكفاءةالفحص وتقليلالضوضاء。 الخصائصالمرنةللبولي يوريثينتمكنألواح الشاشةمنالاهتزاز بتردد أعلى، مما يحسن فصلالجزيئاتالدقيقة ويزيدالإنتاجية。 بالإضافةإلىذلك، تساهمخصائصتخميد المادةفيتقليل مستويات الضوضاءبشكل كبير أثناء التشغيل، ممايعززالسلامة والراحةفيمكانالعمل。 في المقابل، تولد المواد التقليديةمثل الشبكات السلكية مستوياتأعلىمن الضوضاء وقد لا تحقق نفس المستوىمندقة الفحص。
علىالرغممنهذه المزايا،منالضروري مراعاةالمتطلبات المحددةلكلتطبيقعند اختيارمادةالغربلة。 فيحينأنشبكةالبولي يوريثينتوفرأداءً فائقًافيالعديدمن الجوانب، إلاأنهناك سيناريوهات قد تكون فيهاالموادالتقليدية أكثرملاءمة。 على سبيل المثال، في التطبيقات التي تنطوي علىدرجاتحرارةعالية للغاية، قد تتفوق الشاشات المعدنيةعلى مادةالبولييوريثين بسببارتفاعنقطة انصهارها。 فصلالموادوتصنيفها。 بفضلمتانتها الاستثنائية، ومقاومتهاالبيئية، وخيارات التخصيص، والكفاءةالتشغيلية، تبرزغربلةالبولي يوريثينكخيارمتميز لمجموعةواسعةمن التطبيقاتالصناعية。 ومع ذلك، ينبغي دائمًا أنيتماختيارمواد الفحصالأكثرملاءمة بالاحتياجاتوالظروف المحددةلكلتطبيق،مما يضمنالأداءالأمثل والفعاليةمنحيث التكلفة。
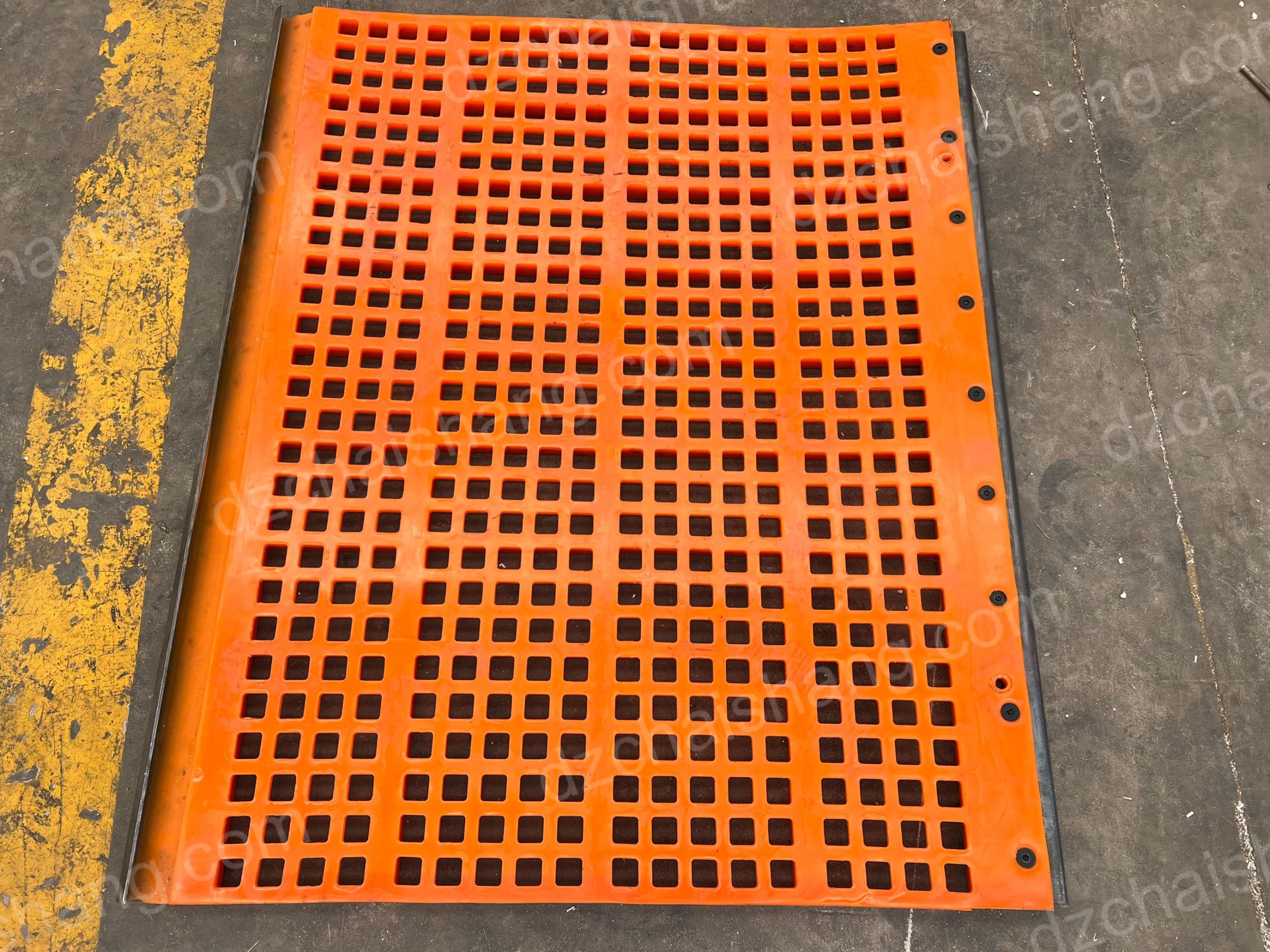
聚氨酯网的另一个显着优势是其灵活性和定制选项。聚氨酯可以模制成各种形状、尺寸和配置,从而可以定制满足特定筛选要求的解决方案。这种适应性对于需要精确颗粒分离和尺寸分类的应用特别有利。另一方面,传统筛分材料提供的定制选项有限,通常需要在效率和效果方面做出妥协。
聚氨酯筛网在筛分效率和降噪方面也表现出色。聚氨酯的弹性特性使筛板能够以更高的频率振动,从而改善细颗粒的分离并提高产量。此外,该材料的阻尼特性有助于显着降低操作过程中的噪音水平,从而提高工作场所的安全性和舒适度。相比之下,丝网等传统材料会产生更高水平的噪音,并且可能无法达到相同水平的筛分精度。
尽管有这些优点,但在选择筛选材料时,必须考虑每种应用的具体要求。虽然聚氨酯网格在许多方面提供了优越的性能,但在某些情况下传统材料可能更合适。例如,在涉及极高温度的应用中,金属筛网由于其熔点较高,可能优于聚氨酯。
总而言之,聚氨酯筛网和传统筛网材料之间的比较凸显了聚氨酯技术为筛网领域带来的显着进步和优势。物料分离和分类。凭借其卓越的耐用性、耐环境性、定制选项和运行效率,聚氨酯筛网成为各种工业应用的绝佳选择。然而,选择最合适的筛分材料应始终以每种应用的具体需求和条件为指导,确保最佳性能和成本效益。