橡胶筛网、聚氨酯筛网、聚氨酯筛板
مزاياالشاشات المطاطيةفيتطبيقات الغربلةالصناعية
تبرزالشاشات المطاطية، المعروفة بمتانتهاالاستثنائية ومقاومتهاللتآكل، كخيارمثاليلتطبيقات الفحصالشاقة。 تسمح المرونةالمتأصلة للمطاطلهذهالشاشات بامتصاصالصدمات،مما يقللمناحتماليةالكسر وإطالةعمرها الافتراضي。 لاتعملهذهالمرونةعلى تعزيزالكفاءة التشغيليةلعمليات الفحص فحسب، بل تقلل أيضًامنتكاليف الصيانةبشكلكبير،مما يجعلالشاشاتالمطاطية حلاً فعالاً من حيث التكلفةلصناعاتمثل التعدينوالمحاجر وإعادةالتدوير。
علاوة علىذلك،توفرالشاشات المطاطيةإمكانات فائقةلتقليلالضوضاء مقارنةبالشاشات المطاطية。 نظرائهمالمعدنية。 تعملالتركيبةالكثيفة للمطاطعلىتخفيف الاهتزازبشكلفعال وتقليلانبعاثاتالصوت أثناءعمليةالغربلة。 تعتبرهذهالميزةمفيدة بشكلخاصفيالمناطق الحضريةأوالمكتظة بالسكان، حيث قد تؤدي لوائح التلوث الضوضائي إلىتقييدساعاتالعمل أوتتطلباتخاذتدابير إضافيةلعزلالصوت。 منخلالتخفيفمستويات الضوضاء، تمكنالشاشات المطاطيةالصناعاتمن العمل بشكل أكثر تكتمًا والامتثالللمعايير البيئية،وبالتالي تعزيزعلاقةمتناغمةمع المجتمعات المحيطة。
بالانتقالإلىشاشات وألواح الشاشة المصنوعةمنالبولي يوريثين،تشتركهذه البدائلفيبعضالخصائص المفيدةللشاشات المطاطية، مثلالمتانة وتقليلالضوضاء،مع تقديمفوائدإضافية أيضًا。 تشتهر شاشات البولي يوريثينبمقاومتها العاليةللتآكل،مما يجعلهامناسبةبشكل استثنائي للتطبيقات التي تتضمن مواد حادة أو كاشطة。 تعملمقاومةالمادة للتآكلعلىإطالةعمر خدمة الشاشات، مما يضمن أداءً ثابتًابمرور الوقت。
تمتصميملوحات الشاشات المصنوعةمن مادة البولي يوريثين، علىوجهالخصوص،لسهولة التركيبوالاستبدال。 تسمح طبيعتها المعياريةبإجراء تغييرات سريعةوسهلة، مما يقلل من وقت التوقف عنالعملويعزز الإنتاجية。 علاوةعلىذلك،يمكن تخصيصهذهاللوحات لتناسبمتطلباتالفحص المحددة،بمافيذلك الأحجاموالأشكال وتكويناتالفتحة المختلفة。 تضمنهذهالقدرةعلى التكيفإمكانيةتصميم ألواح شاشة البولي يوريثينلتلبية المتطلبات الفريدة لتطبيقاتالفحص المختلفة، بدءًامنفصل الجسيمات الدقيقةإلى سلخ فروة الرأس للخدمة الشاقة。
في الختام، تقدم كل من الشاشات المطاطية وشاشات البولي يوريثين،بمافيذلك ألواح شاشة البولي يوريثين،نطاقًامن المزاياالتيتجعلها مناسبةللغاية لتطبيقاتالفحص الصناعي。 ويعتمد الاختياربين هذهالموادعلى المتطلبات المحددة لعمليةالغربلة،بمافي ذلكطبيعةالموادالتي يتم فحصها، والمتانة والعمرالمطلوبين للغرابيل،وأي اعتباراتبيئيةمثل تقليلالضوضاء。 ومنخلالالاستفادةمن الخصائصالفريدة للمطاطوالبولي يوريثين،يمكن للصناعات تحسينعمليات الفحصالخاصةبها، وتحقيقكفاءةأعلى، وخفضتكاليفالصيانة، وتحسينالامتثال البيئي。 معتقدمالتكنولوجيا، يستمرتطويرحلولالفحص المبتكرةفيتعزيزأداء واستدامةالعمليات الصناعيةفيجميعأنحاء العالم.
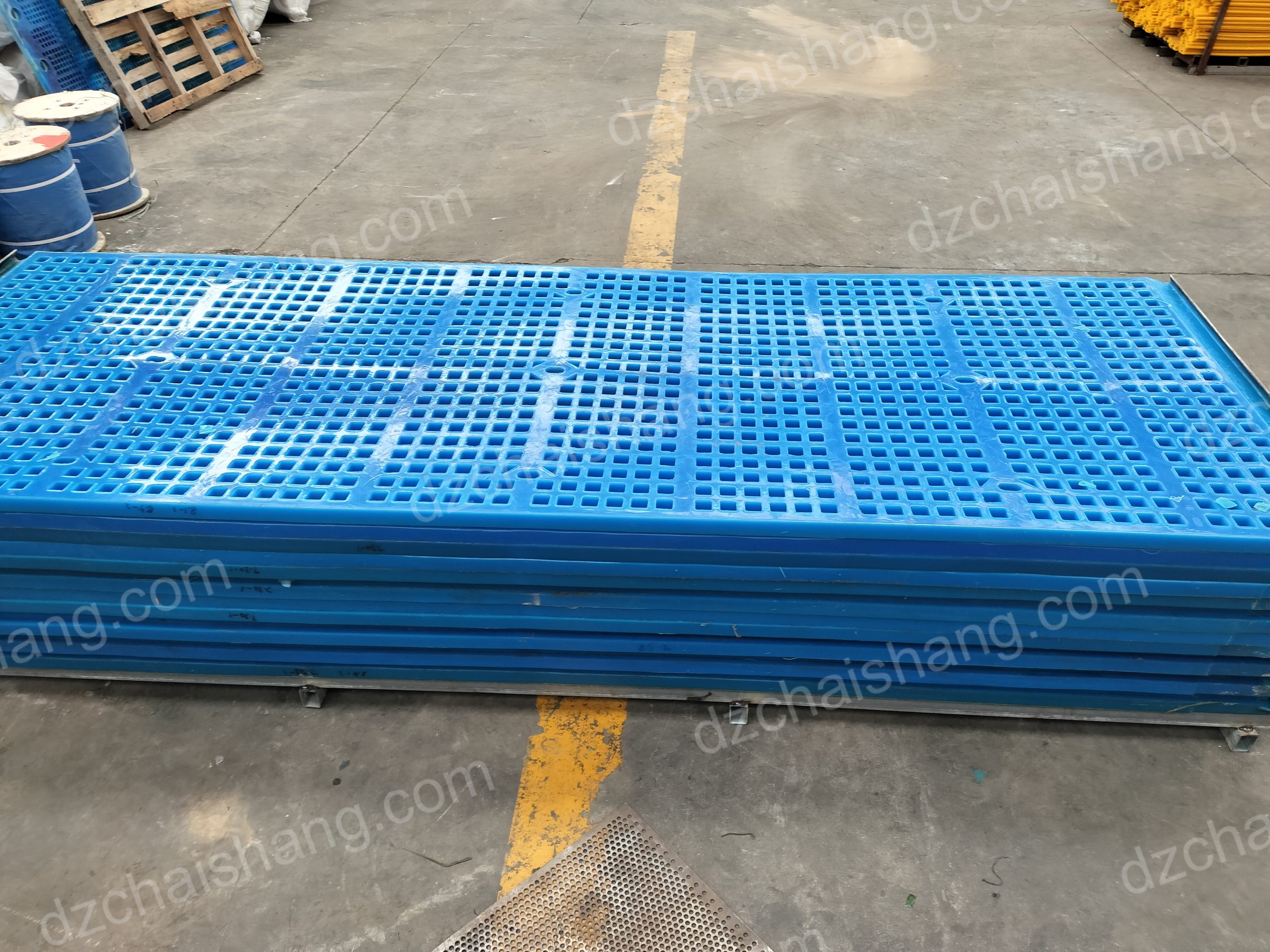
مزاياالشاشات المطاطيةفيتطبيقات الغربلةالصناعية
شاشات البولي يوريثين: تعزيزالكفاءة والمتانةفيعمليات الغربلة
شاشات البولي يوريثين: تعزيزالكفاءة والمتانةفيعمليات الفحص
في مجال فصل المواد وتصنيفها، تلعب كفاءةوسائطالفحصوطول عمرهاأدوارًامحورية فيالنجاحالتشغيلي。 منبينالخيارات المختلفةالمتاحة، برزت شاشات البولي يوريثينكخيارمتميز، حيث توفر مزيجًا من المرونةوالمتانة والأداءالعاليالذي تكافح الشاشات المطاطيةالتقليديةأو الشبكات السلكيةمنأجل مطابقته。 تم تصميم ألواح شاشات البولي يوريثين المبتكرةهذهلتتحمل قسوةتطبيقاتالفحص الشاقة، مما يجعلها عنصرًالاغنىعنهفي الصناعات التي تتراوح منالتعدينإلى المعالجةالإجمالية。
تبدأالمزاياالكامنة في شاشات البولي يوريثينببنائها。 علىعكسالشاشات المطاطية، التي يمكن أن تكونعرضةللتآكل،فإن مادةالبولييوريثينهي مادةمرنةللغايةتقاوم التآكلوالتمزق والتأثير。 تُترجمهذهالمتانةإلى عمر خدمة أطول، مما يقلل منتكرارعمليات استبدالالشاشةوتقليل وقت التوقفعنالعمل。 وبالتالي،يمكن للعمليات الحفاظعلى إنتاجيةثابتة،مما يضمنبقاءالإنتاجية عاليةمعالحفاظعلى تكاليفالصيانةتحت السيطرة。
علاوةعلىذلك، توفر شاشات البولي يوريثينأداءًفائقًا في تطبيقات الغربلة الرطبة。 تمنعطبيعتهاغير المساميةالتشبع بالمياه،وهيمشكلة شائعةفي الشاشات المطاطيةالتييمكنأن تؤدي إلى العمى وتقليل كفاءةالفحص。 مقاومةالبولييوريثين الممتازةللماءتعني أيضًاأنهأقلاحتمالًا لإيواءالبكتيرياأو الطحالب، الأمر الذي يمكن أن يكون مصدر قلق في بيئات معينة حيث تكون النظافةذاتأهميةقصوى。
منالمزاياالمهمة الأخرى لألواح شاشة البولي يوريثين هي تعدد استخداماتها。 يمكنتصنيعهابمجموعة واسعةمنأحجاموأشكال الفتحات،ممايلبي متطلبات الفحصالمحددة。 سواء كانت المهمة تنطوي علىفصلالجسيمات الدقيقةأوالتعاملمع المواد الخشنة، يمكن تخصيص شاشات البولي يوريثينلتحسينعملية الفحص。 ويمتد هذا التخصيص إلى الأبعادالمادية للشاشةوأنظمة التثبيت،ممايضمن ملاءمةمثاليةلأيسطح عرضوسهولة التركيب.
تسمحمرونة تصميمشاشاتالبولي يوريثينأيضًابدمج الميزات التي تعزز كفاءةالفحص。 علىسبيلالمثال،تم تصميمبعضألواحشاشات البولي يوريثينبفتحات مدببةتسهلمرورالمواد وتقللمناحتمالية الانسداد。 قد يتميز البعض الآخر بمناطقمعززةحيثيكون التآكلأكثركثافة،مما يطيلعمرالشاشةبشكل أكبر。
بالإضافةإلى سماتهاالعملية،تساهم شاشات البولي يوريثين فيالاستدامةالبيئية。 وتعني متانتهاأنها تحتاج إلى الاستبدال بشكلأقلتكرارًامن الأنواعالأخرىمن الشاشات، مما يؤدي إلى تقليلالنفايات。 علاوةعلىذلك،نظرًا لأن البولي يوريثين عبارةعنبوليمرمتصلد بالحرارة، فهو لا يذوب ويمكنطحنهوإعادة استخدامهفينهايةدورة حياته، مما يوفر خيارًا أكثرصداقةللبيئة للتخلصمنهمقارنة بالمواد الأخرى.
الانتقالمن الحواجزالمطاطية التقليديةإلىشاشات البولي يوريثينهي شهادةعلىالتقدمفي تكنولوجياالفحص。 لميقمالمشغلونالذين قاموابإعدادتقرير التبديلبتحسينالأداء فحسب، بل قاموا أيضًا بتوفيركبيرفي التكاليفبمرورالوقت。 يتم تعويض الاستثمار الأولي في ألواح شاشات البولي يوريثينبسرعة منخلالتقليلالصيانة وانقطاعات التشغيل، مما يثبت أن هذه الشاشات هي خيار ذكي لأي مؤسسة تتطلعإلىتحسينعمليات الفحصالخاصةبها。
في الختام، تمثلشاشات البولي يوريثينقفزة إلىالأمامفيالفحص تكنولوجياوسائل الإعلام。 إنمتانتهاوكفاءتها وقدرتهاالاستثنائية علىالتكيفتجعلهاحلاً مثاليًالمجموعةواسعة منتحدياتالفحص。 معاستمرارالصناعاتفي البحث عن طرق لتحسين عملياتهاوخفض التكاليف، فمنالواضح أن ألواح شاشات البولي يوريثينستلعبدورًا متزايد الأهميةفي مستقبلفصلالمواد。
聚氨酯筛网:提高筛分操作的效率和耐用性
在材料分离和分类领域,筛分介质的效率和寿命在操作成功中发挥着关键作用。在各种可用的选择中,聚氨酯筛网已成为一种优越的选择,它兼具灵活性、耐用性和高性能,这是传统橡胶筛网或金属丝网难以比拟的。这些创新的聚氨酯筛板经过精心设计,能够承受重型筛分应用的严酷考验,使其成为从采矿到骨料加工等行业不可或缺的组件。
聚氨酯筛板的固有优势始于其结构。与容易磨损的橡胶筛网不同,聚氨酯是一种高弹性材料,可抵抗磨损、撕裂和冲击。这种韧性意味着更长的使用寿命,减少筛网更换频率并最大限度地减少停机时间。因此,操作可以保持一致的吞吐量,确保保持高生产率,同时控制维护成本。此外,聚氨酯筛网在湿式筛分应用中提供卓越的性能。它们的无孔特性可以防止积水,这是橡胶筛网的常见问题,可能导致堵塞和筛分效率降低。聚氨酯优异的耐水性还意味着它不太可能含有细菌或藻类,而细菌或藻类在清洁和卫生至关重要的某些环境中可能会成为一个问题。
聚氨酯筛板的另一个显着优点是其多功能性。它们可以制造成各种孔径尺寸和形状,以满足特定的筛选要求。无论任务涉及细颗粒分离还是粗糙材料的处理,都可以定制聚氨酯筛网以优化筛分过程。这种定制延伸到屏幕的物理尺寸和紧固系统,确保完美适合任何屏幕面板并易于安装。
除了实用属性之外,聚氨酯屏幕还有助于环境的可持续性。它们的耐用性意味着它们需要比其他类型的屏幕更换频率更低,从而减少浪费。此外,由于聚氨酯是一种热固性聚合物,它不会熔化,可以在其生命周期结束时被磨碎并重新利用,与其他材料相比,提供了更环保的处置选择。
从传统橡胶筛网到聚氨酯筛网是筛分技术进步的证明。进行了转换的运营商表示,随着时间的推移,不仅提高了性能,而且还显着节省了成本。对聚氨酯筛板的初始投资很快就被维护和操作中断的减少所抵消,这证明这些筛子对于任何希望增强筛分操作的组织来说都是明智的选择。
总而言之,聚氨酯筛子代表了筛分领域的一次飞跃媒体技术。其卓越的耐用性、效率和适应性使其成为应对各种筛选挑战的理想解决方案。随着各行业不断寻求优化流程和降低成本的方法,聚氨酯筛板显然将在未来的材料分离中发挥越来越重要的作用。