maille vibrante, panneaux de criblage modulaires
تطورشبكةالغربلة الاهتزازية:التطورات والتطبيقات
تطورشبكةالغربلة الاهتزازية:التطورات والتطبيقات
فيمجالفصل المواد وتحجيمها، تلعب شبكةالغربلة الاهتزازيةدورًا =
ألواح الغربلةالمعيارية: =
ألواح الغربلة المعيارية:إحداثثورة في كفاءة فصل المواد
في مجالفصلالمواد وتحجيمها، كانظهور لوحات الغربلة المعياريةبمثابةقفزة كبيرةإلىالأمامفي الكفاءةوالفعالية。 لقد غيرت هذه الأنظمة المبتكرةالطريقةالتي تتعاملبهاالصناعاتمع عمليةالغربلة،مما يوفرمستوىمنالقدرة علىالتكيفوالأداء الذي لا يمكن لشبكة الغربلةالاهتزازية التقليديةأنتضاهيه。 بينمانتعمقفيتعقيدات لوحات الغربلة المعيارية،يصبحمن الواضح لماذاأصبحت الخيارالمفضلللعديد منالعمليات。
الميزة الأساسيةلألواح الغربلةالمعيارية تكمنفيتعدد استخداماتها。 علىعكسشبكةالغربلة الاهتزازيةالسلكية المنسوجةالتقليدية، والتي عادةً ما تكونتصميمالألواح المعياريةلتكونقابلة للتبديلبسهولة。 وهذايسمحبإجراء تعديلات سريعة لاستيعابالمواد المختلفةأوالتغييرات فيعمليةالإنتاج。 إنالقدرةعلىتبديل اللوحات بسرعة لا تقلل منوقتالتوقفعنالعمل فحسب،بلتمكّن المشغلينأيضًامنضبط عمليةالفحصلتحقيق نتائج فصلمثالية。
منالمزاياالرئيسية الأخرى للوحات الغربلة المعياريةهيمتانتها。 تم تصميم هذه الألواح، المصنوعةمنمواد متقدمةمثلالبولي يوريثينأوالمطاطأو الفولاذ المقسى، لتحمل قسوةالفحصالشاق。 وتترجممرونةهذه المواد إلى عمر أطول للألواح، وهو ما يعني بدورهعددًاأقلمن عمليات الاستبدال وانخفاضتكاليف الصيانةبمرورالوقت。 تعد هذه المتانة أمرًا بالغ الأهمية بشكل خاص في الصناعات التي تنتشر فيهاالموادالكاشطةأو القوىعاليةالتأثير، حيث إنها تضمن أداءًالصعبة。
يساهمتصميم لوحات الغربلة المعياريةأيضًافي تحسينكفاءةالفحص。 يمكنتصنيعالألواح بمجموعةمتنوعةمن التشكيلات السطحية،أوذاتالأنماط المتخصصة، لتعزيز تدفق الموادوفصلها。 بالإضافةإلىذلك،يمكن تزويد الألواح بميزاتالمنزلقةلتحسينعملية الفحصبشكلأكبر。 تعمل عناصر التصميمهذه بشكلمتضافرلمنعحدوث مشكلات مثل التعمية والربط، والتي يمكن أن تعيقبشكلكبيركفاءة شبكةالغربلة الاهتزازية。
علاوةعلى ذلك، يعد التأثير البيئي لألواح الغربلة المعياريةجانبًالا يمكنإغفاله。 نظرًالأنالصناعات أصبحت تدرك بشكل متزايد بصمتهاالبيئية،فإن إمكانيةإعادة الاستخداموإعادة التدويرللألواح المعياريةتمثلخيارًا أكثراستدامةمقارنة بشبكات الشاشة التقليدية。 إنالقدرةعلىاستبدال الأجزاءالباليةفقط بدلاً من الشاشات بأكملهاتقللمنالهدر، وغالبًامايتماختيار المواد المستخدمة في الألواح المعيارية وفقًالتوافقها البيئي.
يعدتركيبلوحات الغربلةالمعيارية مجالًا آخر تتفوق فيه علىنظيراتها التقليدية。 تسمح بساطةأنظمة اللوحات بالتركيب السريعوالسهل،غالبًا دونالحاجةإلىأدوات متخصصةأوتدريبمكثف。 إنسهولةالتثبيتهذهلا توفر الوقت فحسب، بل تقللأيضًامناحتمالية حدوث أخطاء قد تؤثر على عمليةالفحص。
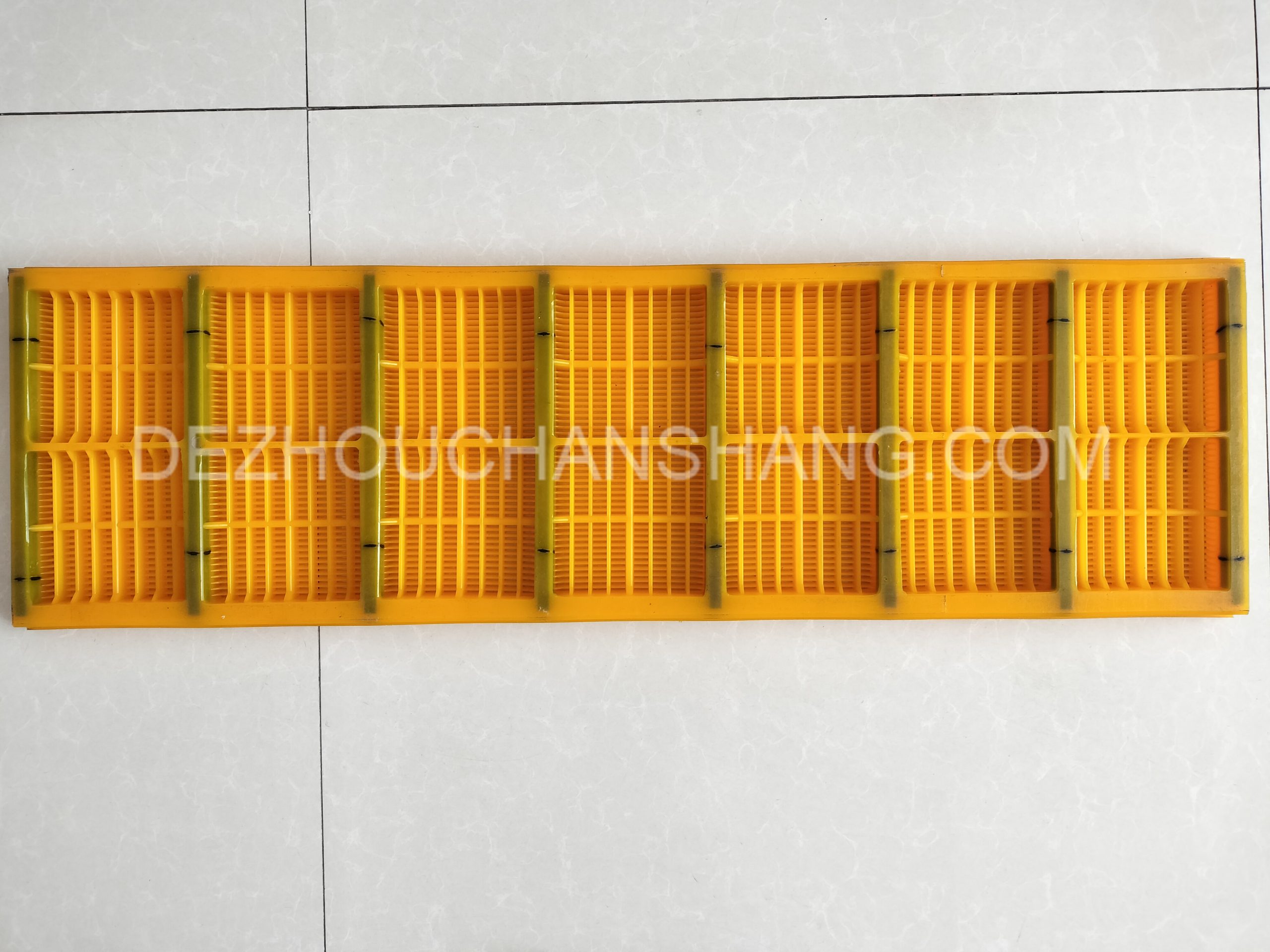