湿物料筛分用高弹性聚氨酯筛板
فوائد وتطبيقات ألواح غربلةالبولييوريثين عاليةالمرونةفيغربلة الموادالرطبة
تُحدث ألواح الشاشة المصنوعةمنمادة البولي يوريثينعالية المرونةثورةفيعملية غربلةالموادالرطبة، حيث تقدم مجموعة من الفوائد التي تجعلها خيارًامثاليًالمختلف التطبيقاتالصناعية。 هذهالألواحمصنوعةمن مادة البولي يوريثين، وهوبوليمرمتعدد الاستخداماتمعروف بمرونتهالاستثنائية ومقاومتهللتآكل。 وهذايجعلهامناسبة بشكلخاصللظروفالصعبة التي غالبًا ما تواجهها عمليات غربلةالمواد الرطبة.
إحدىالمزايا الأساسيةلألواحغربال البولي يوريثينعالية المرونةهيمتانتها الفائقة。 يمكنأنتتحللمواد الشاشةالتقليدية،مثل الشبكات السلكية، بسرعةتحتالتأثير الكاشطللموادالرطبة。 وفي المقابل، فإن المتانةالمتأصلةفي مادةالبولييوريثين تسمح لها بتحمل التعرض لفترات طويلةللعناصر القاسيةدونفقدان سلامتهاالهيكلية。 لاتعملهذهالمتانةعلى إطالةعمرألواح الغربلةفحسب،بلتقلل أيضًامنالحاجةإلى الاستبدالات المتكررة، مما يؤدي إلى توفير كبير في التكاليف بمرورالوقت.
علاوةعلى ذلك، تلعبالمرونة العاليةلألواحالبولي يوريثانهذهدورًا حاسمًافيتعزيزكفاءة الغربلةعملية。 تسمح الطبيعةالمرنة للمادةبامتصاص الصدمات والاهتزازات، ممايساعدعلىمنع التعميةوانسدادفتحات الشاشة。 ونتيجةلذلك،تحافظ الألواح على أداء ثابت وموثوقحتىعندالتعامل معالموادذاتالمحتوى العاليمنالرطوبة。 وهذايضمنبقاءعملية الغربلةدونانقطاع، وبالتاليزيادة الإنتاجية والإنتاجية.
منالمزايا الرئيسيةالأخرى لاستخدامألواحالشاشة المصنوعةمنمادة البولي يوريثينعالية المرونة هو ملف تعريف السلامةالمحسن。 يقللالسطحالأكثر نعومةمنمادةالبولي يوريثينمنخطرإصابة العمالالذينيتعاملون معالشاشات،مقارنة بالحوافالحادةالتي توجدغالبًاعلى الشاشاتالمعدنية。 بالإضافةإلىذلك، تساهممستوياتالضوضاء المنخفضةالمرتبطة بشاشات البولي يوريثين في توفير بيئة عمل أكثر أمانًاوراحة。
مقارنةألواحغربلة البولي يوريثينعالية المرونةمعمواد الغربلةالأخرى
نصائح لصيانة ألواح شاشات البولي يوريثين عاليةالمرونة
أولاً،منالمهمفحص لوحات الشاشةبانتظام بحثًاعنأيعلاماتتآكل أوتلف。 ابحث عن التمزقات أو الثقوبأوأيمناطققد ينفصلفيهاالبولي يوريثينعنالإطار。 يمكن أن يؤدي اكتشاف هذه المشكلات مبكرًاإلى منعالمزيدمنالضرر وتجنبعمليات الاستبدالالمكلفة。 بالإضافةإلىذلك،تحقق منعدموجودأيتراكم للمواد على سطح الشاشة، لأن ذلك يمكن أن يقلل من كفاءةالغربلةويضع ضغطًاإضافيًاعلى اللوحة。
يعد تنظيف لوحات الشاشة جانبًامهمًاآخرمن جوانبالصيانة。 معمرورالوقت،يمكنأن تستقرالجزيئاتفي فتحات الشاشة، مما يقلل منفعاليتها。 لتنظيفالألواح، استخدمفرشاةناعمةأو رذاذ ماء منخفض الضغط لإزالةأيحطام。 تجنباستخدامالماء عالي الضغط أو أدوات التنظيفالكاشطة،حيث يمكن أن يؤدي ذلك إلى إتلاف مادة البولي يوريثين。 منالمهمأيضًاالتأكد منأنالألواحجافة تمامًاقبلإعادة تثبيتها، حيث يمكن أن تتسببالرطوبةفيتدهور المادةبمرورالوقت。
يعد التثبيت والشد المناسبينلألواح الشاشةأيضًامن العواملالرئيسيةفي الحفاظعلىأدائها。 عند تثبيت الألواح، تأكدمنتثبيتهابشكل آمنوشدهابالتساوي。 وهذايساعدعلىمنع الترهلويضمنتوزيع المواد بالتساوي عبر الشاشة。 قمبفحصشدالألواحبشكل دوري واضبطهاحسب الضرورةللحفاظعلى كفاءةالفحص المثلى。
نصيحةالصيانة المهمةالأخرىهي مراقبةظروفتشغيل معداتالفحص。 يمكنأنتساهمدرجات الحرارةالمرتفعة والاهتزازالمفرط والتعرضللمواد الكيميائيةفيتدهور ألواح شاشات البولي يوريثين。 تأكدمنأنالمعداتتعمل ضمنالمعلماتالموصى بهامنقبلالشركة المصنعةواتخذالخطوات اللازمةللتخفيفمنأي ظروفمعاكسة。 على سبيل المثال، يمكن أنيساعدتركيبمخمدات الاهتزازأواستخدام موادمقاومةللحرارة علىحمايةالألواحمن التلف.
أخيرًا،منالمهم الاحتفاظبسجللأنشطة الصيانةواستبدال اللوحات。 يمكنأنيساعدكهذافي تحديدالأنماطأو المشكلات المتكررة، مما يسمح لك باتخاذ إجراءات استباقيةلمنع حدوث مشكلات في المستقبل。 يمكنأنيساعدكتتبع العمرالافتراضيلكل لوحةأيضًافيالتخطيط لعمليات الاستبدال والميزانيةوفقًا لذلك。
في الختام، يتطلب الحفاظعلىألواحشاشة البولي يوريثينعالية المرونةإجراءفحص منتظموتنظيفوتركيب مناسبومراقبةظروف التشغيلوحفظالسجلات。 باتباعهذهالنصائح، يمكنكالتأكدمن استمرارأداءلوحات الشاشةبكفاءة وفعالية،ممايقللوقت التوقفعنالعملويوفر التكاليفعلىالمدى الطويل。 تذكرأنالصيانة الوقائيةهيالمفتاح لإطالةعمرمعدات الغربلةالخاصةبك وتحقيقالنتائج المثاليةفيغربلة المواد الرطبة.
高弹聚氨酯筛板的维护技巧
高弹性聚氨酯筛板广泛应用于采矿和集料行业中湿物料的筛分。这些面板以其耐用性、效率以及降低噪音和振动的能力而闻名。然而,为了确保它们继续发挥最佳性能,适当的维护至关重要。通过遵循一些简单的技巧,您可以延长高弹性聚氨酯筛板的使用寿命并保持其有效性。
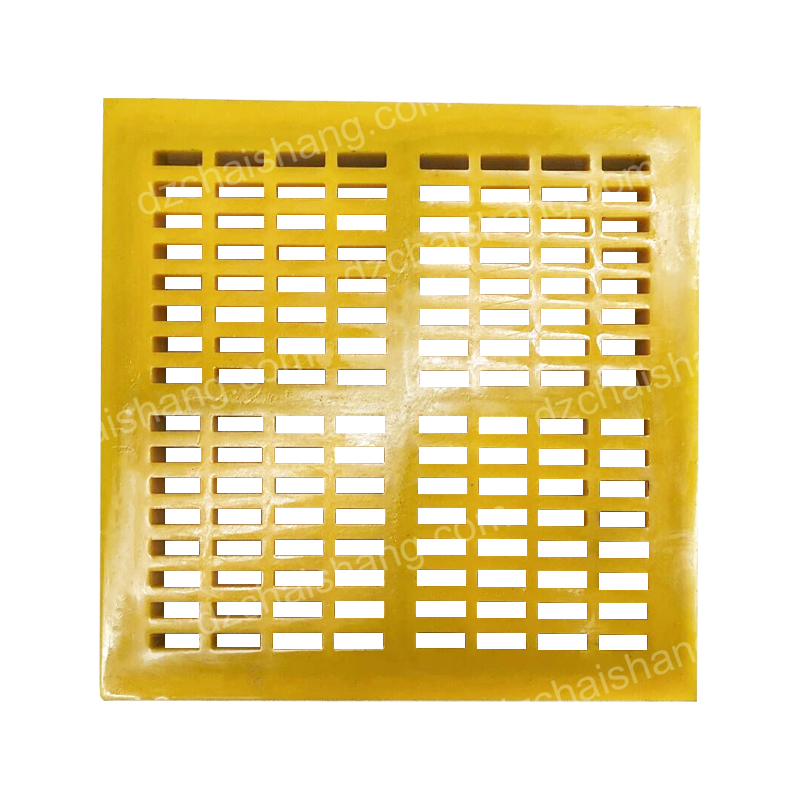
首先,定期检查屏幕面板是否有任何磨损或损坏的迹象非常重要。寻找撕裂、孔洞或聚氨酯可能与框架分离的任何区域。尽早发现这些问题可以防止进一步的损坏并避免昂贵的更换。此外,检查筛子表面是否有任何堆积的材料,因为这会降低筛分效率并对面板施加额外的压力。
清洁筛板是维护的另一个重要方面。随着时间的推移,颗粒可能会滞留在屏幕的开口中,从而降低其有效性。要清洁面板,请使用软刷或低压水喷雾清除任何碎屑。避免使用高压水或研磨性清洁工具,因为它们会损坏聚氨酯材料。在重新安装面板之前确保面板完全干燥也很重要,因为水分会导致材料随着时间的推移而降解。
筛板的正确安装和张紧也是保持其性能的关键因素。安装面板时,确保面板紧固牢固且张紧均匀。这有助于防止下垂并确保材料均匀分布在屏幕上。定期检查面板的张力并根据需要进行调整,以保持最佳的筛选效率。
另一个重要的维护技巧是监控筛选设备的运行状况。高温、过度振动和接触化学品都会导致聚氨酯筛板的降解。确保设备在制造商建议的参数范围内运行,并采取措施减轻任何不利条件。例如,安装减振器或使用耐温材料有助于保护面板免受损坏。
最后,保留维护活动和面板更换的记录也很重要。这可以帮助您识别模式或重复出现的问题,使您能够采取主动措施来防止未来出现问题。跟踪每个面板的使用寿命还可以帮助您相应地计划更换和预算。
总之,维护高弹性聚氨酯筛板需要定期检查、清洁、正确安装、监控操作条件和保存记录。通过遵循这些提示,您可以确保您的屏幕面板继续高效且有效地运行,从长远来看,减少停机时间并节省成本。请记住,预防性维护是延长筛分设备使用寿命并在湿材料筛分中实现最佳结果的关键。