振动筛中的聚氨酯筛网聚氨酯振动筛
فوائد استخدام شاشات البولي يوريثينفي المناخلالاهتزازية
نصائح الصيانة للمناخل الاهتزازيةمنمادة البولي يوريثين
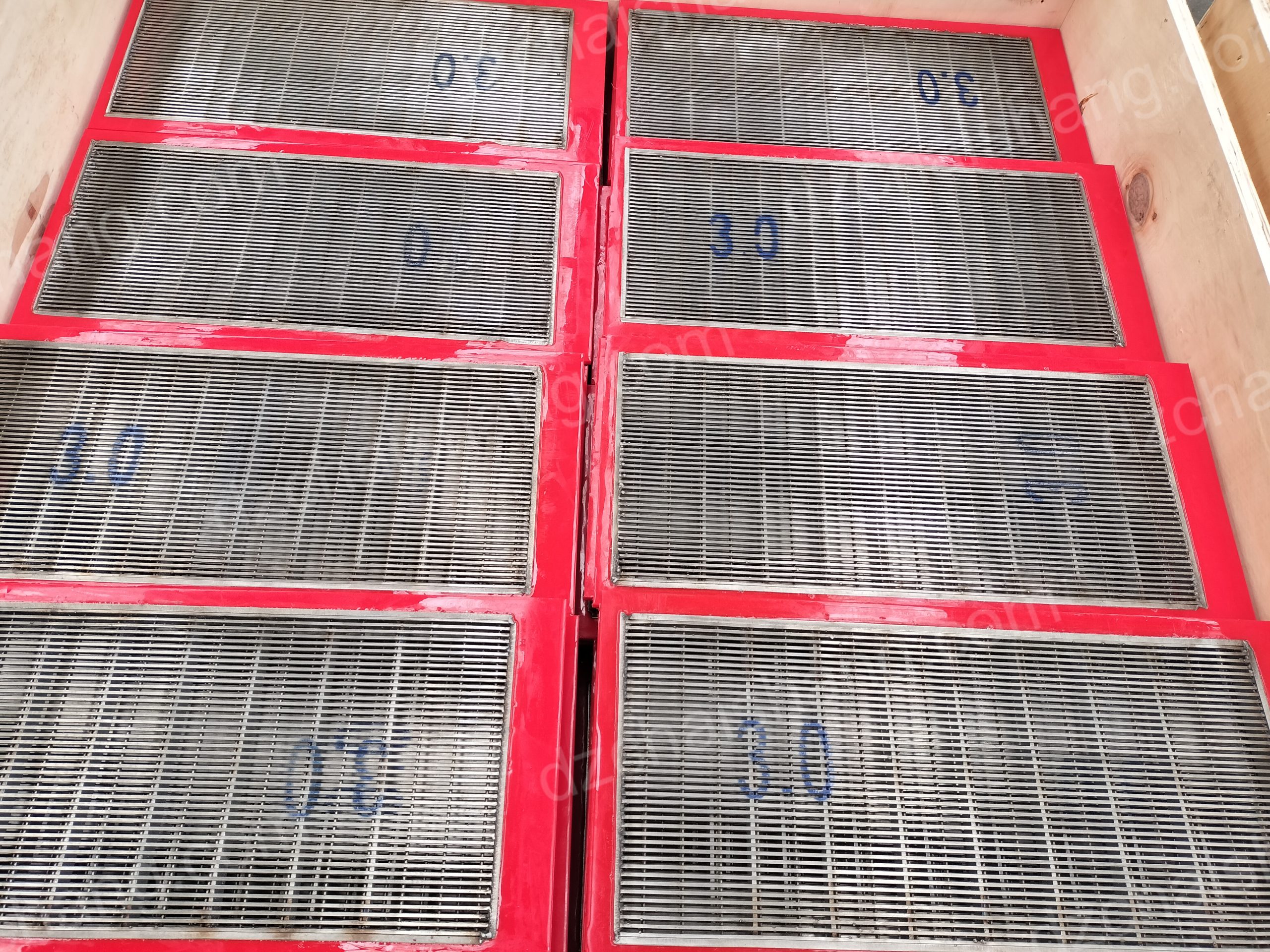
تُستخدمغرابيل الغربلةالاهتزازيةمن مادةالبولييوريثين علىنطاقواسعفيصناعات التعدينوالركامنظرًا لمتانتهاالعالية وكفاءتهاومقاومتها للتآكلوالتآكل。 تعتبرهذهالمناخل مكونات أساسية للغرابيلالاهتزازية التي تساعد في فرز المواد المختلفة وتحجيمهاوفصلها。 لضمانالأداءالأمثل وطولعمرغرابيل الغربالالاهتزازيةمن مادة البولي يوريثين، تعد الصيانة الدورية أمرًابالغالأهمية。 منخلالاتباعبعضنصائح الصيانةالبسيطة،يمكن للمشغلينزيادة الكفاءةإلىأقصىحد وإطالة عمر أدوات الفحص القيمةهذه.
أولاً،من المهمفحصشاشةالبولي يوريثينبانتظامبحثًا عنأيعلاماتتآكلأوتلف。 يتضمنذلكالتحققمنعدم وجود تمزقات أو ثقوب أو أيتشوهاتعلىسطح المنخل。 يسمح الاكتشافالمبكر لمثلهذهالمشكلات بإجراءالإصلاحاتأو الاستبدالاتفيالوقت المناسب،ممايمنع المزيدمنالضرر واحتمالالتوقفعن العمل。 ومنالضروريأيضًا التأكد من شد الشاشة ومحاذاتهابشكلصحيح。 يمكن أن يؤدي الشد غير الصحيح إلى التآكل المبكر، في حين أن المحاذاةغيرالصحيحة يمكن أن تسبب توزيعًا غير متساوٍ للمواد على الشاشة، ممايقللمن فعاليتها。
يعدتنظيف غربالالغربال الاهتزازيمنمادة البولي يوريثينممارسة صيانةحيويةأخرى。 معمرورالوقت،قد يتراكمعلىالشاشة الغباروالجسيمات وغيرهامنالحطامالذي يمكن أن يسد الفتحات ويقللمنكفاءةالفحص。 يساعدالتنظيفالمنتظم فيالحفاظعلىفتحات واضحةللتحجيموالفصل الدقيق。 يوصىباستخدامطرق التنظيفالمناسبةمثل الغسيلبالماءأو استخداممحاليل التنظيفالمتخصصة، وذلكحسبنوعالمادة التي تتم معالجتها ومستوىالتلوث。
علاوة على ذلك، من المهم مراعاةظروفالتشغيل التي يهتز فيها البولي يوريثان يتم استخدام غربالالشاشة。 يمكن أن تؤثر عوامل مثل سعةالتحميلوتكرار الاهتزازوالسعةبشكل كبيرعلىمعدلتآكل الشاشة。 يساعدتشغيلالغربال ضمنالمعلماتالمحددة منقبلالشركةالمصنعة علىتقليلالضغطوالضغط علىالمادة،وبالتالي تقليلخطرالفشلالمبكر。 بالإضافةإلىذلك،يجب تدريبالمشغلينعلى مراقبة هذه الإعدادات وضبطهاحسبالحاجة للتكيفمعمتطلبات المعالجةالمتنوعة。 تساعد ظروف التخزين المناسبةمثلالبيئة النظيفةوالجافة والتحكمفيدرجة الحرارةعلىالحفاظعلى سلامةمادةالبولي يوريثين。 يجب أيضًا توخي الحذر أثناءالتعامللتجنبأي تأثيرات حادة أو انحناء مفرط قد يؤدي إلى تلف الشاشة。 منخلالتنفيذممارسات التخزينوالتعامل المناسبة،يمكن للمشغلينالتأكدمنأن الشاشات الاحتياطيةفي حالةمثاليةعندالحاجة للاستبدال。
وأخيرًا، يُنصح بالاحتفاظبسجل لأنشطة الصيانة، بما في ذلكعملياتالفحص والتنظيفوالإصلاحات والاستبدال。 تساعدهذهالوثائقفي تتبعالأداءوأنماط التآكللغرابيل الغربلةالاهتزازيةمن مادةالبولييوريثينمع مرورالوقت。 يمكن أن يوفر تحليل هذه السجلات رؤى قيمة حول العواملالتيتؤثرعلى عمرالغرابيلوتوجيه ممارسات الصيانة المستقبلية。 منخلالإجراءعمليات الفحصالروتيني، وتنظيفالشاشات، والتشغيلضمنالمعلمات الموصى بها، وتخزين الشاشات الاحتياطية والتعاملمعهابشكل صحيح، والاحتفاظ بسجلات الصيانة التفصيلية،يمكن للمشغلينتحسينأداء شاشات الاهتزاز الخاصة بهم وتقليل وقت التوقف عنالعمل。 لاتساهمهذهالممارسات فيالتشغيلالسلس لعمليةالغربلةفحسب، بلتؤديأيضًاإلىتوفير كبيرفيالتكاليفمن خلالإطالةعمرخدمة مناخلالبولي يوريثين.
مقارنةبين شاشات البولي يوريثين وموادالشاشةالأخرى
إحدىالفوائدالأساسية لشاشات البولي يوريثين هي مقاومتها الاستثنائيةللتآكل。 مصنوعة من مادة البولي يوريثينشديدةالتحمل، يمكنلهذهالشاشاتأن تتحملالظروفالقاسية والمواد الكاشطة دون أن تتمزقأوتنكسر。 وهذهميزةكبيرةمقارنة بالشاشات الشبكية السلكية، والتي يمكن أن تعانيبسهولةمن التآكل، مما يؤدي إلى عمليات استبدالمتكررة وزيادة وقت التوقف عن العمل。 بالإضافةإلىذلك،تعد شاشات البولي يوريثين أكثرمقاومةللتآكل والعواملالبيئية الأخرى، مما يزيد من طول عمرهاالافتراضي。
الميزةالأخرىلشاشات البولي يوريثينهي كفاءةالفحصالفائقة。 تسمح الخصائصالفريدة للبولي يوريثينبأحجام فتحةأكثردقة واتساقًا، مما يؤدي إلى فصلوتصنيفأفضلللمواد。 وهذامهمبشكلخاصفي الصناعات التي تكون فيهادقةحجمالجسيمات أمرًابالغ الأهمية، كماهوالحالفيمعالجة المعادنأوالأدوية。 في المقابل، غالبًا ما تحتوي شاشات الشبكات السلكيةعلىمخالفاتفي فتحاتها، مما يؤدي إلى نتائج فحص أقل دقة。
توفر شاشات البولي يوريثين أيضًاتقليلًاأفضل للضوضاءمقارنة بالموادالأخرى。 تساعدالمرونة المتأصلةفيمادة البولي يوريثينعلى امتصاصالاهتزازات وتقليلمستويات الضوضاءأثناءعملية الغربلة。 وهذهفائدةكبيرةفي البيئات التي يكون فيها التلوث الضوضائي مصدر قلق، كما هو الحال في المناطقالحضريةأو بالقربمنالمناطق السكنية。 منناحيةأخرى،تميل الشبكات السلكية وشاشات الألواح المثقبةإلىأنتكون أكثرضوضاءًبسبب هياكلهاالصلبة،والتي يمكنأنتضخم الاهتزازات والصوت.
علاوةعلىذلك، تعد شاشات البولي يوريثينأكثرمرونة وقدرةعلىالتكيفمع تطبيقات الفحص المختلفة。 يمكنتصميمهابمجموعة واسعةمنالأشكال والأحجاموالتكوينات لتناسبالاحتياجات المحددة。 تسمح هذهالمرونة بالحلولالمخصصةالتي يمكنهاتحسينأداء الفحصوكفاءته。 علىالرغممنأنالشاشات المطاطيةمرنةأيضًا، إلا أنها قد لا تقدم نفس المستوىمنالتخصيص والدقةمثلشاشات البولي يوريثين。
فيما يتعلقبالصيانة،فإن شاشات البولي يوريثين أسهلفي التعاملمعها وتتطلبعملياتاستبدال أقلتكرارًا。 إنمتانتهاومقاومتها للتآكلتعنيأنهايمكن أن تدوم لفترة أطول دون الحاجةإلىإصلاحاتأو استبدال。 يمكن أن يؤدي ذلك إلى توفير كبير في التكاليف بمرورالوقت،حيثيتم تقليلالنفقات المرتبطةبصيانة الشاشةووقتالتوقفعن العمل。 في المقابل، قد تتطلب الشبكات السلكية والشاشات المطاطية صيانة واستبدالات أكثر تكرارًا،ممايزيدمن تكاليفالتشغيل。
على الرغممنهذهالمزايا، منالمهممراعاة المتطلبات المحددةلكل تطبيقعنداختيارمادة الشاشة。 في حين أن شاشات البولي يوريثينتقدمالعديدمن الفوائد، فقد تكون هناك حالات تكون فيها مواد أخرى، مثل الشبكات السلكيةأوالألواح المثقبة، أكثرملاءمة بسببعواملمثلالتكلفة أوالتوفرأوخصائص الموادالمحددة。
في الختام، توفر شاشات البولي يوريثينقوة والحلالفعالللمناخل الاهتزازية،ممايوفر مقاومةفائقةللتآكل، وكفاءةالغربلة، وتقليلالضوضاء، والمرونة، وسهولة الصيانة。 عند مقارنتهابمواد الشاشات الأخرى، تتميز شاشات البولي يوريثين بمتانتهاوأدائها،مما يجعلها خيارًاقيمًا لمجموعةواسعةمن التطبيقاتالصناعية。 ومع ذلك، فإن الدراسة الدقيقةللاحتياجات والظروفالمحددةلكل عمليةغربلةأمرضروري لضمانالاختيارالأمثل لمواد الغربلة.
聚氨酯筛网与其他筛网材料的比较
聚氨酯筛网因其耐用性和筛选过程的效率而在各个行业中越来越受欢迎。与其他筛网材料(例如丝网、橡胶或穿孔板)相比,聚氨酯筛网具有多种优势,使其成为振动筛的首选。
聚氨酯筛网的另一个优点是其卓越的筛分效率。聚氨酯的独特性能允许更精确和一致的孔径尺寸,从而更好地分离和分类材料。这对于粒度精度至关重要的行业尤其重要,例如矿物加工或制药行业。相比之下,金属丝筛网的开口通常不规则,导致筛分结果不太准确。
与其他材料相比,聚氨酯筛网还可以提供更好的降噪效果。聚氨酯固有的弹性有助于吸收筛选过程中的振动并降低噪音水平。这对于关注噪音污染的环境(例如城市地区或靠近住宅区)来说是一个显着的好处。另一方面,丝网和穿孔板筛网由于其刚性结构而往往噪音较大,这会放大振动和声音。此外,聚氨酯筛网更灵活,可适应各种筛分应用。它们可以设计成各种形状、尺寸和配置,以满足特定需求。这种灵活性允许定制解决方案,从而优化筛选性能和效率。橡胶筛网虽然也很灵活,但可能无法提供与聚氨酯筛网相同水平的定制和精度。
在维护方面,聚氨酯筛网更容易处理,并且需要较少的更换频率。它们的耐用性和耐磨损性意味着它们可以使用更长时间,而无需维修或更换。随着时间的推移,这可以显着节省成本,因为与屏幕维护和停机时间相关的费用会减少。相比之下,金属丝网和橡胶筛网可能需要更频繁的维护和更换,从而增加了运营成本。
尽管有这些优点,但在选择筛网材料时,重要的是要考虑每种应用的具体要求。虽然聚氨酯筛网具有许多优点,但在某些情况下,由于成本、可用性或特定材料特性等因素,其他材料(例如丝网或穿孔板)可能更合适。
总而言之,聚氨酯筛网提供了坚固的振动筛的高效解决方案,具有卓越的耐磨性、筛分效率、降噪性、灵活性和易于维护性。与其他筛网材料相比,聚氨酯筛网因其耐用性和性能而脱颖而出,使其成为各种工业应用的宝贵选择。然而,仔细考虑每个筛选过程的具体需求和条件对于确保筛选材料的最佳选择至关重要。