批发筛网尺寸,脱水筛设计,振动筛网中国
فهمأحجامشاشات الشبكات بالجملة:دليل شامل
الابتكارات في تصميم شبكات نزح المياه وتصنيعشبكاتالغربال الاهتزازيةفيالصين
الابتكارات في تصميم شاشات نزح المياه وتصنيعشبكاتالغربال الاهتزازيةفي الصين
شهدمجالفصل المواد ونزح المياه تطورات كبيرةفي السنوات الأخيرة، لا سيما في تصميم شاشات نزح المياهوتصنيعشبكات الغربالالاهتزازية。 كانت الصين، باعتبارها قوةصناعيةعالمية،في طليعةهذهالابتكارات، مما دفع حدود الكفاءة والفعاليةفيالصناعة。
أصبحت أحجام الشاشات الشبكيةبالجملة متنوعةبشكلمتزايد لتلبيةالاحتياجات المتنوعةلمختلف الصناعات。 منالمساحيقالدقيقة إلى الركام الخشن، أتاحت القدرة على تخصيص حجمفتحاتالشبكةإجراء عملياتفصلأكثردقة。 لايقتصرهذاالتخصيص علىالأبعادفحسب،بل يشملأيضًاشكل الفتحات، والتي يمكن أن تكونمربعةأومستطيلة أوحتىممدودةلتناسب خصائصالموادالمحددة بشكلأفضل。
لقدتطور أيضًاتصميمشاشاتنزح المياه。 تم تصميم شاشات نزح المياهالحديثةلتوفير قوةجاذبيةعالية واهتزازات سريعةتسهل حركةالماءبعيدًاعن المواد。 يعد هذا أمرًا بالغ الأهميةفيالصناعات التي يمكن أن يؤثر فيها محتوىالرطوبةبشكل كبيرعلىجودةالمنتج النهائي أو قابليته للاستخدام،كماهو الحالفيعمليات التعدينوالرملوالحصى وإدارةالنفايات。 أدت تحسينات التصميم إلى ظهور شاشات ليست أكثرفعاليةفيإزالة المياهفحسب،بلأيضًا أكثر كفاءة في استخدام الطاقة، ممايقللمن تكاليفالتشغيل للشركات。
علاوةعلىذلك،شهدت المواد المستخدمة في بناءالشاشةترقيات。 يتم استخدام الفولاذ عالي القوة والبولي يوريثينبشكلشائع لمتانتهماومقاومتهما للتآكل。 تضمنهذهالموادقدرة الشاشات على تحمل الظروفالقاسية والكاشطةالتيغالبًا ماتوجدفيتطبيقاتنزح المياه، وبالتالي إطالةعمرالمعدات وتقليلوقتالتوقفعن العملللصيانة.
كماتبنى تصنيعشبكاتالغرابيل الاهتزازيةفيالصين التقدمالتكنولوجي。 أدىاستخدامآلات النسيج الآليةواللحام الدقيقإلىالحصولعلى شبكات ذات دقة أبعاد عاليةواتساق。 يعدهذاالمستوىمن الدقةضروريًاللحفاظ علىأداءالغرابيل الاهتزازية،حيثأن المخالفات الطفيفة يمكن أن تؤدي إلى انخفاض الكفاءةواحتمالتلوث المواد。
بالإضافةإلىالجوانب الماديةلتصميمالشاشة وتصنيعالشبكات،تمدمج البرامج والأدوات الرقميةفيالعملية。 تسمح برامج المحاكاة للمهندسينبنمذجةسلوك المواد على الشاشات، ممايمكنهممنتحسين التصميملتطبيقات محددةقبلإنشاء النماذج الأولية المادية。 وهذالايوفرالوقت والموارد فحسب، بل يؤدي أيضًاإلىإنتاجمنتجات ذات أداء أفضل يمكن طرحهافي السوقبسرعة أكبر。
ويتجلىالتزامالصين بالابتكارفيهذا المجالفيالاستثمار المستمرفيالبحث والتطوير。 يتعاونالمصنعونفي البلاد مع المؤسسات الأكاديميةوخبراء الصناعةلاستكشافمواد جديدةوتقنياتالتصنيع ومبادئالتصميم。 يضمنهذاالنهج التعاوني بقاءالصناعة الصينيةفيطليعة تكنولوجياشاشاتنزح المياهوشبكاتالغربلة الاهتزازية.
فيالختام، أدت التطورات في تصميم شاشات نزح المياه وتصنيعشبكاتالغربال الاهتزازيةفيالصين إلىالمزيدمنالكفاءة والمتانةوالتكلفة -حلولفعالةلفصلالمواد ونزحالمياه。 ومنخلالالتركيزعلى التخصيصوعلومالمواد والتكاملالرقمي، تواصل الصين وضع معايير الابتكارفيهذاالقطاع الصناعيالحيوي。
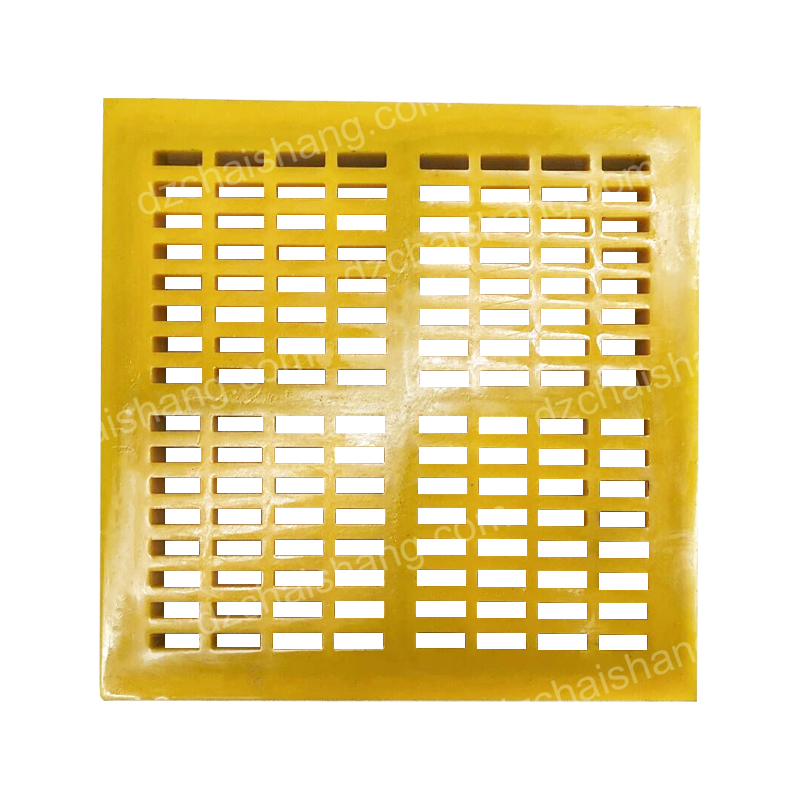
网布的表面处理也受到关注。采用镀锌、涂防腐材料等工艺,增强网片的防锈、防腐蚀能力。这在筛网暴露于水或其他腐蚀性物质的应用中尤其重要。
除了筛网设计和筛网制造的物理方面之外,软件和数字工具也已集成到该过程中。仿真软件允许工程师在屏幕上对材料的行为进行建模,使他们能够在构建物理原型之前优化特定应用的设计。这不仅节省了时间和资源,而且还可以带来性能更好的产品,从而可以更快地推向市场。
中国对这一领域创新的承诺体现在对研发的持续投资上。该国的制造商正在与学术机构和行业专家合作,探索新材料、制造技术和设计原理。这种协作方式确保了中国工业始终处于脱水筛和振动筛网技术的前沿。
总而言之,中国脱水筛设计和振动筛网制造的进步带来了更高效、更耐用和更低成本的产品。 -有效的材料分离和脱水解决方案。中国专注于定制、材料科学和数字集成,不断为这一关键行业领域的创新树立标准。